Agitators Technology
Top Entry Agitators
Top entry agitators are industrial mixing devices used to blend and homogenize liquids and suspensions within tanks or vessels.
They are characterized by their positioning on the top of the tank, where the agitator shaft extends downward into the liquid. The working principles of top entry agitators involve the following key aspects:
Design: A typical top entry agitator consists of an agitator shaft connected to a motor and impeller. The agitator is mounted on the top of the tank or vessel, with the impeller submerged in the liquid.
Agitation: When the motor is activated, it drives the agitator shaft and impeller. The impeller’s rotation generates fluid motion, creating turbulence and promoting mixing within the tank.
Flow Patterns: Top entry agitators create various flow patterns, including axial flow (up and down movement of fluid along the shaft), radial flow (outward and inward movement from the center), and tangential flow (circular movement along the tank wall). These flow patterns help disperse and mix materials effectively.
Speed and Direction: The speed and direction of the impeller’s rotation can be adjusted to achieve the desired mixing intensity and pattern. Different impeller designs are available to suit specific applications
Material Compatibility: Top entry agitators are constructed from materials compatible with the substances being mixed to ensure corrosion resistance and durability.
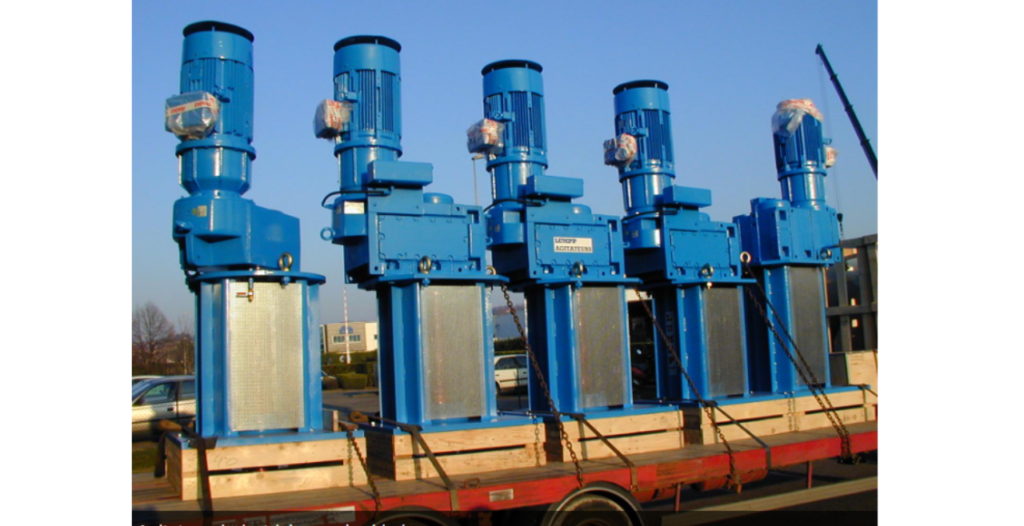
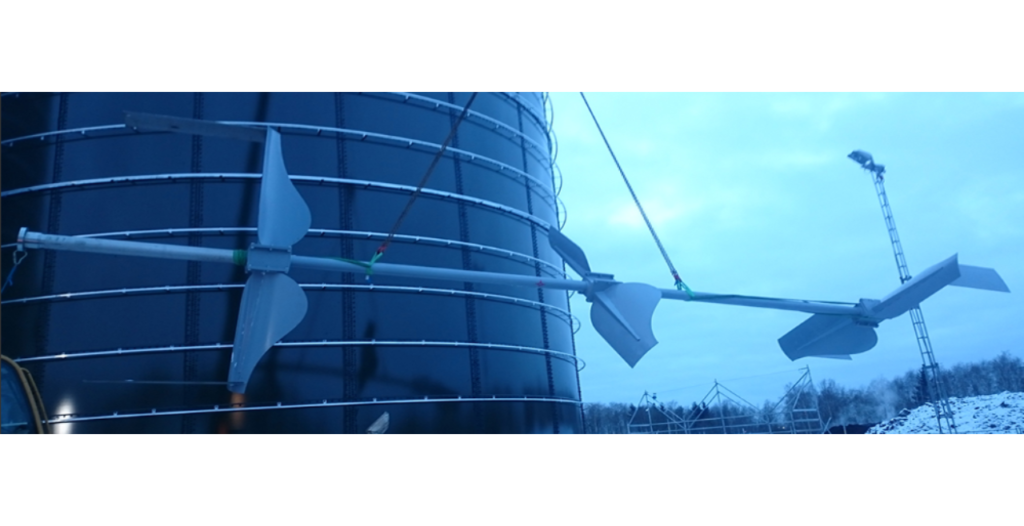
Advantages:
Effective Mixing: Top entry agitators provide efficient mixing, making them suitable for various applications, from blending chemicals to suspending solids in liquids.
High Capacity: They are capable of handling large tank volumes, making them ideal for industrial processes requiring substantial quantities of mixing.
Customizable: Top entry agitators can be tailored to suit specific applications by selecting the appropriate impeller design and adjusting speed and direction.
Reduced Sedimentation: They help prevent settling and sedimentation of particles in the bottom of the tank, maintaining product consistency.
Low Maintenance: With proper maintenance, top entry agitators have a long service life and require minimal downtime.
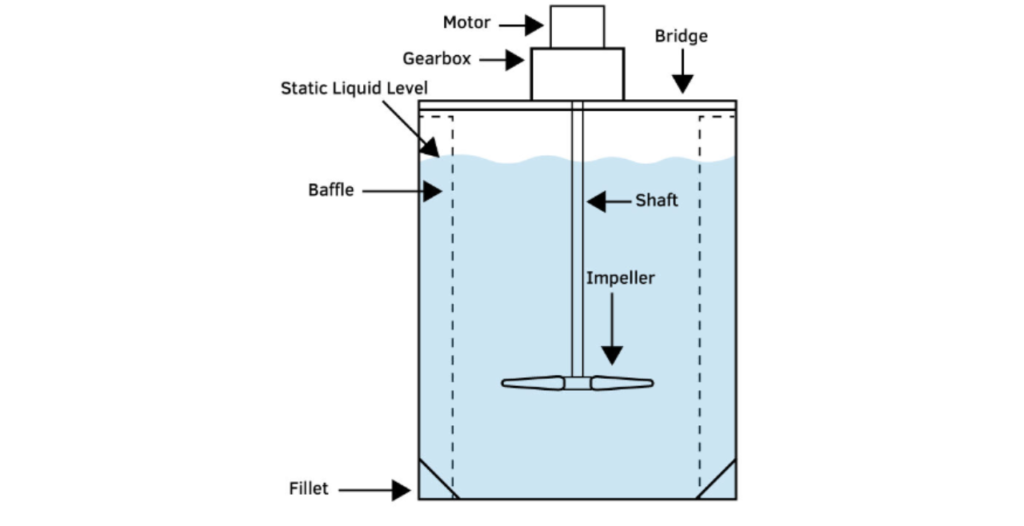
Disadvantages:
Space Requirements: Top entry agitators may require substantial headroom above the tank, which can be a limitation in certain installations.
Initial Cost: The purchase and installation of top entry agitators can have higher upfront costs compared to some other mixing methods.
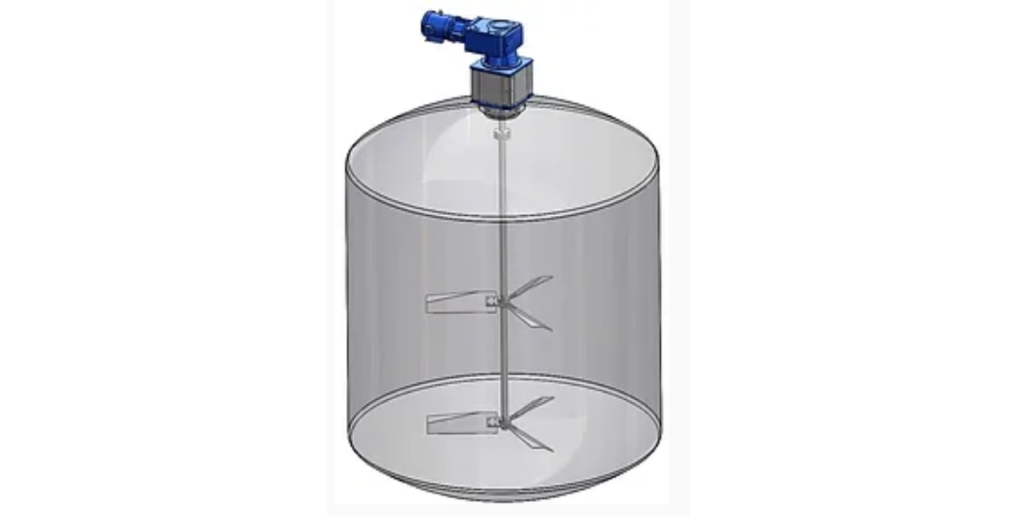

Applications: Top entry agitators are used in a wide range of industries and applications, including:
Chemical processing: Mixing chemicals, polymers, and pharmaceuticals.
Oil and gas: Homogenizing crude oil, blending petroleum products, and suspending solids.
Water and wastewater treatment: Agitating and mixing in water treatment processes.
Food and beverage: Mixing ingredients in food processing and dairy applications.
Pulp and paper: Stirring pulp and paper pulp stock in paper manufacturing.
Mining and minerals: Mixing and suspending ores and minerals in mineral processing.
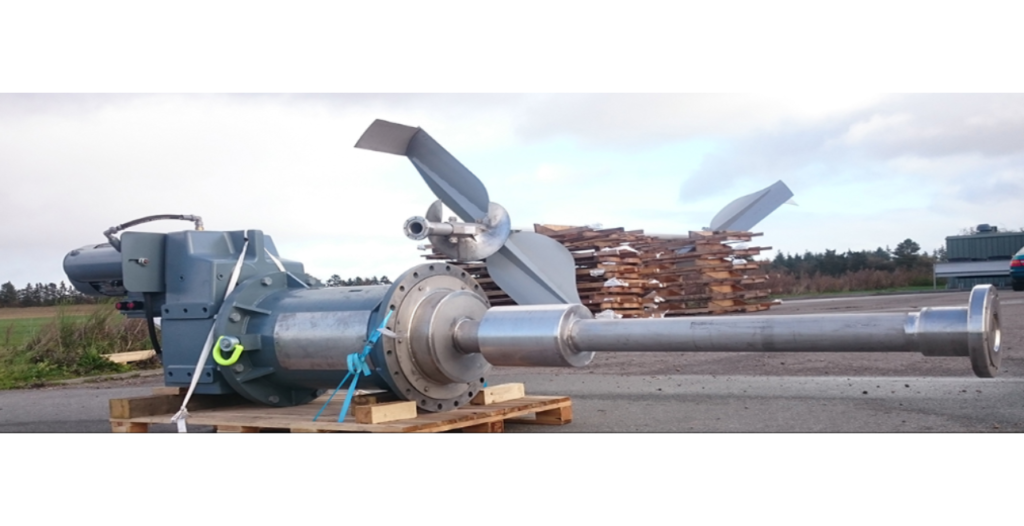
Summary: Top entry agitators are versatile industrial mixing devices that provide efficient and effective blending and suspension of materials within tanks and vessels.
They offer advantages such as high capacity, customization options, and low maintenance requirements. However, they may require substantial space and involve higher initial costs.
Top entry agitators find applications in various industries, including chemical processing, oil and gas, water treatment, food and beverage, pulp and paper, and mining.
Their ability to create effective flow patterns makes them essential for achieving uniform mixing and product consistency in numerous industrial processes.