Mixers/Blenders Technology/Products
Plough Shear Mixers
Plough shear mixers, also known as plow mixers or ploughshare mixers, are specialised blending and mixing devices used in various industries to combine dry powders, granules, and other solid materials.
They are known for their unique plough-shaped mixing elements (blades or ploughs) that rotate within a horizontal cylindrical vessel. Here’s an overview of their working principle, advantages, and disadvantages.

Working Principle: The working principle of plough shear mixers involves the rotation of plough-shaped mixing elements within a horizontal vessel. The key working principles include: |
Loading: The dry materials to be blended are loaded into the mixer through an opening at the top. |
Blending: Inside the mixer, multiple plough-shaped mixing elements are mounted on a central shaft. These ploughs rotate at a relatively high speed and are oriented at an angle to the central axis of the vessel. |
Mixing: As the ploughs rotate, they simultaneously lift and tumble the materials in the vessel. The interaction between the ploughs and the materials creates a complex blending action, ensuring that all components are thoroughly mixed. |
Discharging: Once the blending process is complete, the blended mixture can be discharged through an outlet at the bottom of the vessel. |

Advantages of Plough Shear Mixers: |
Uniform Mixing: Plough shear mixers offer excellent mixing uniformity, ensuring that all components are evenly distributed throughout the mixture. |
Versatility: They can handle a wide range of materials, including powders, granules, and materials with varying particle sizes. |
Customization: The design and configuration of the ploughs can be tailored to meet specific blending requirements, making them suitable for various applications. |
High Shear Capability: Plough shear mixers are capable of providing high shear mixing, making them suitable for applications requiring particle size reduction or emulsification. |
Efficient Mixing: They provide efficient blending within relatively short mixing times, reducing processing times and improving production efficiency. |
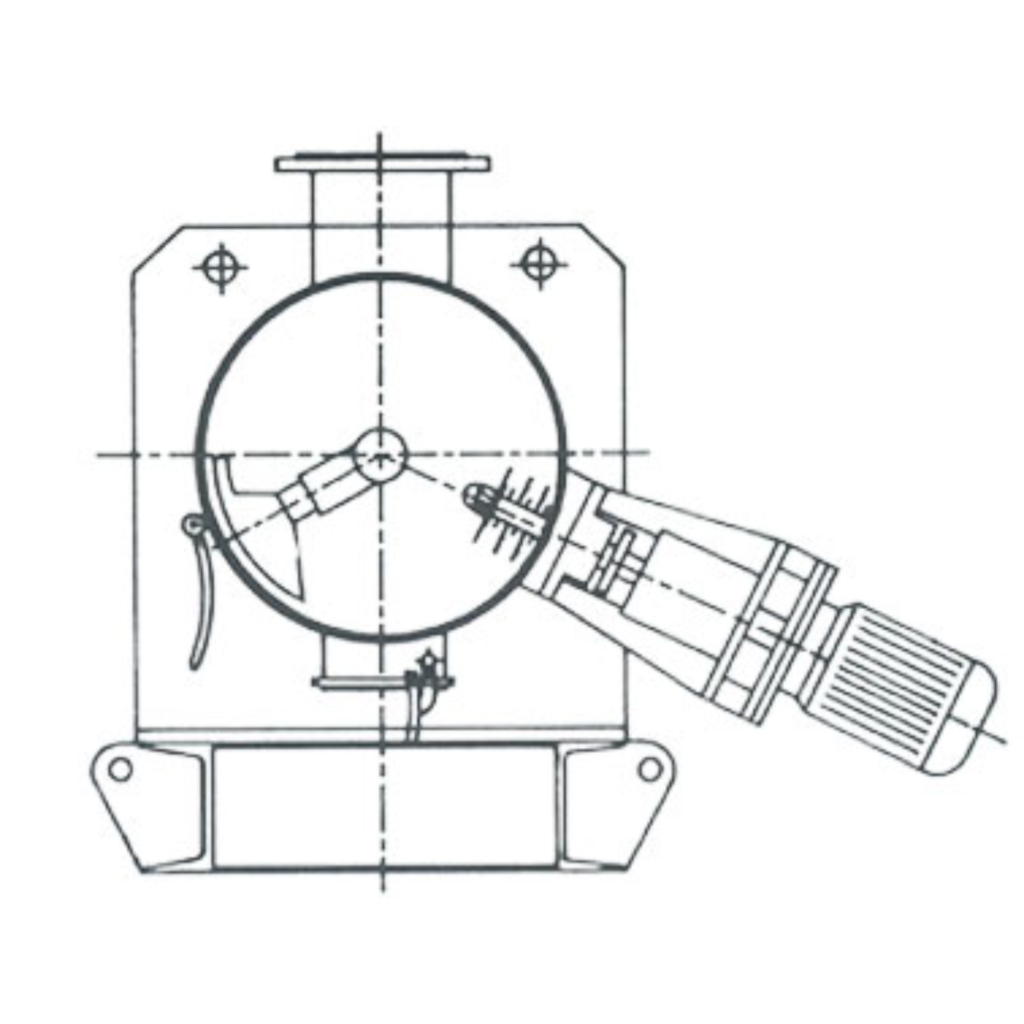
Disadvantages of Plough Shear Mixers: |
Complex Design: The presence of multiple ploughs and the need for a central shaft add complexity to the mixer’s design, which may require more maintenance over time. |
Batch Process: They are typically used for batch processing, which may not be ideal for continuous production lines. |
Potential for Material Buildup: Some materials, especially cohesive or sticky substances, may adhere to the ploughs or the vessel wall, leading to material buildup and uneven mixing. |
Energy Consumption: Achieving the necessary rotation speed for efficient mixing can consume significant energy. |
Limited for Large-Scale Production: Plough shear mixers may not be cost-effective for very large-scale industrial processes due to their batch processing nature. |
In summary, plough shear mixers are effective mixing devices known for their excellent mixing uniformity and versatility. They are particularly suitable for applications that require efficient blending and high shear mixing. However, their complex design and batch processing nature may limit their use in some production scenarios. The choice of mixer type should be based on the specific characteristics of the materials and the blending requirements of the process. |