Rotary Air Valve (RAL)
Drop-Thru Type RAL
Drop-Thru Rotary Airlock Valve is a mechanical device used in material handling and pneumatic conveying systems. Its working principle involves controlling the flow of bulk materials while maintaining an airtight seal between different parts of the system. Here’s how it operates: |
Inlet and Outlet Ports: The valve has an inlet and an outlet. Bulk material enters through the inlet and fills the rotor pockets. |
Rotor with Pockets: Inside the valve, there is a rotating rotor with pockets or chambers. As the rotor turns, the pockets collect and trap the bulk material from the inlet. |
Material Discharge: The rotor continues to rotate, carrying the material within the pockets toward the outlet. When each pocket reaches the outlet, it releases the material into the downstream equipment or process. |
Airtight Seal: The Drop-Thru Rotary Valve is designed to maintain an airtight seal between the inlet and outlet. This sealing prevents air leakage, maintains system pressure, and minimizes dust emissions. |
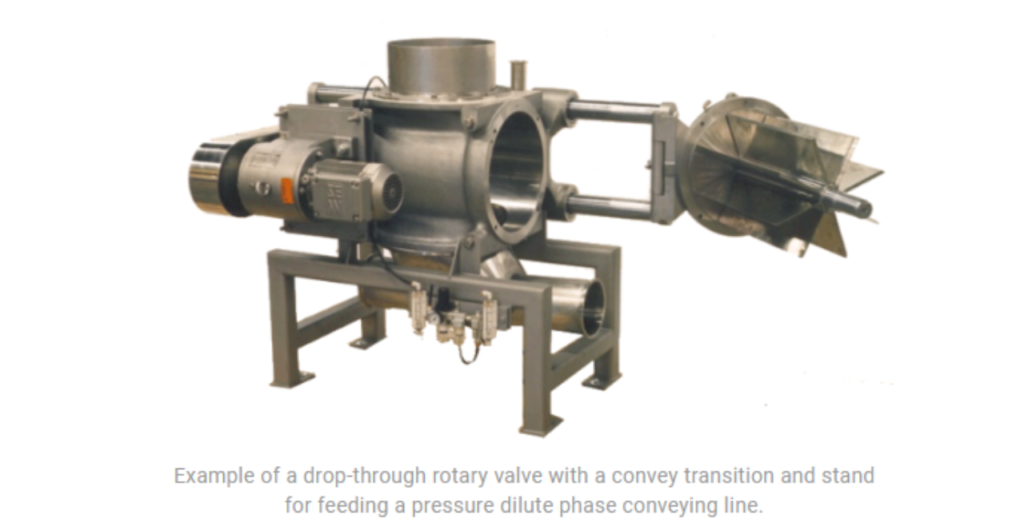
Advantages: |
Material Flow Control: Provides precise control over the flow of bulk materials, allowing for regulated and continuous material transfer. |
Airtight Seal: Maintains an airtight seal between different parts of the system, preventing air leakage and ensuring system efficiency. |
Versatility: Suitable for a wide range of bulk materials, making it versatile for various industries. |
Continuous Operation: Capable of continuous operation, ensuring a steady and controlled material flow. |
Material Segregation Prevention: Helps prevent material segregation by providing uniform discharge of materials into downstream equipment. |
Pressure Maintenance: Maintains desired pressure levels within the system, especially in pneumatic conveying applications. |
The drop-through valve is used mainly for relatively free-flowing, non-cohesive materials such as grain, rice, coffee beans, salt, and sugar. |
With a properly designed adapter feeding material from the valve outlet into the convey line, air leakage across the rotary valve can be reduced in high pressure pneumatic conveyors. This decreases the effects of upward airflow restricting material feed into the valve inlet. |
A drop-through design may be your best option when there are a number of rotary valves in series on a single convey line. In this circumstance, a blow-through design could put too much resistance on the product and cause it to break down, while the obstruction-free convey transition under a drop-through design may better protect the product’s integrity. |
Another benefit of drop-through rotary valves is in applications were cleaning the interior of the valve is essential for product safety. With a drop-through design the internal area of the rotary valve can be accessed without dismantling convey line connections. This makes cleaning quicker and easier. |

Disadvantages: |
Maintenance: Requires regular maintenance to ensure proper functioning, including inspection of rotor vanes, seals, and bearings. |
Material Jamming: Certain materials, such as sticky or abrasive substances, may lead to jamming or wear of the valve components. |
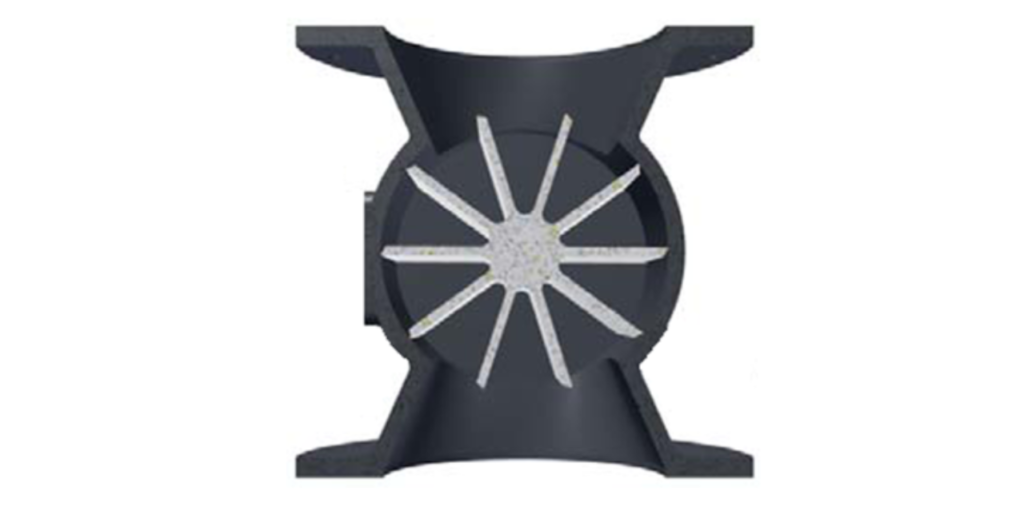
Applications: |
Drop-Thru Rotary Airlock Valves find applications in various industries, including: |
Food Processing: For handling food ingredients, powders, and granules. |
Pharmaceuticals: In pharmaceutical manufacturing for precise material transfer. |
Chemicals: Used in chemical processing to control the flow of chemicals and powders. |
Plastics: In plastics processing for conveying plastic pellets and resin. |
Agriculture: Commonly used in grain handling and feed processing. |
Mining: For handling ores, minerals, and abrasive materials. |
Pneumatic Conveying: Critical components in pneumatic conveying systems to regulate material flow. |

Summary:
A Drop-Thru Rotary Airlock Valve is a vital component in material handling and pneumatic conveying systems. It operates by trapping and releasing bulk materials in pockets as a rotor rotates, maintaining an airtight seal between the inlet and outlet. This design allows for precise material flow control, prevents air leakage, and ensures continuous and efficient material transfer. While versatile and widely used, these valves require regular maintenance to operate effectively in various industries and applications. Proper selection and maintenance are essential for their reliability and performance in industrial processes.