Conical Blenders:
Conical blenders, also known as cone blenders or cone screw blenders, are a type of mixing equipment used in blending technology to combine dry powders and granular materials.
These blenders are characterized by their conical shape and the presence of a helical screw or auger inside. Here’s an overview of their working principle, advantages, and disadvantages:
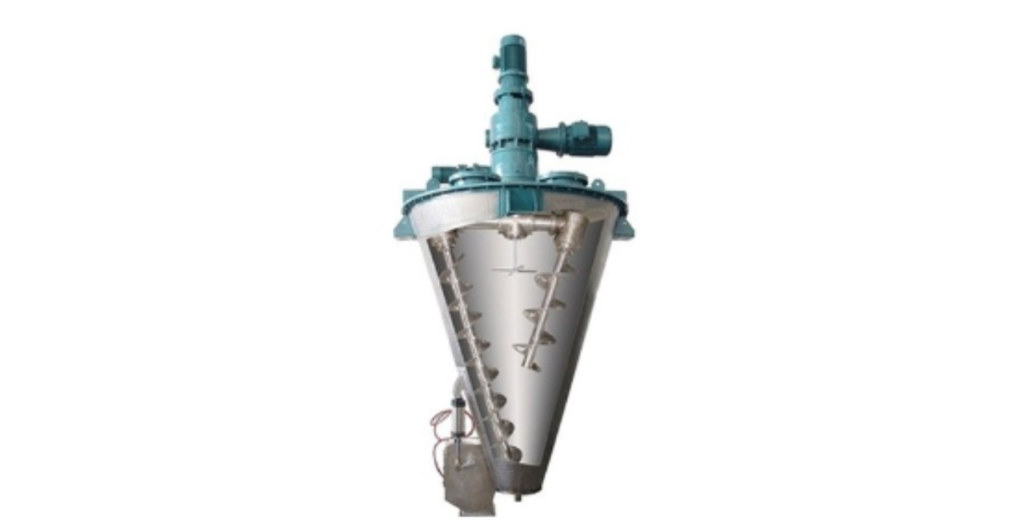
Working Principle: Conical blenders operate on the principle of controlled shear and flow. Here’s how they work: |
Loading: The dry powders or granules to be blended are loaded into the conical blender through an opening at the top. |
Blending: The blender’s helical screw, located within the conical chamber, rotates to lift and gently tumble the materials. This action creates a controlled flow and promotes mixing as the materials cascade and collide with each other. |
Mixing: As the materials move within the blender, they continuously interact with each other, resulting in thorough blending. The controlled shear provided by the screw ensures that even cohesive or difficult-to-blend materials can be mixed effectively. |
Discharging: Once blending is complete, the blended mixture can be discharged through a valve at the bottom of the conical chamber. |
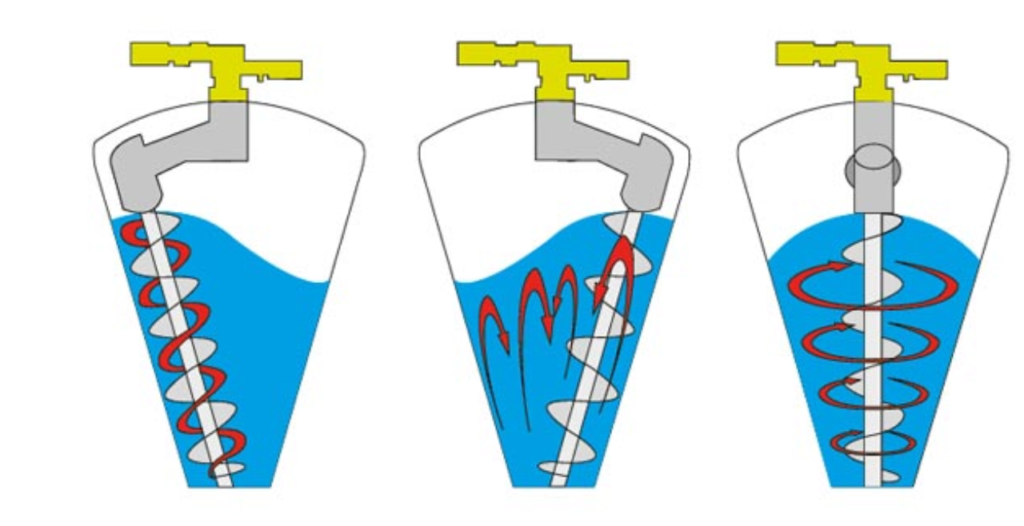
Advantages of Conical Blenders: |
Uniform Mixing: Conical blenders offer excellent mixing uniformity, ensuring that all components are evenly distributed throughout the mixture. |
Efficient for Cohesive Materials: They are particularly well-suited for blending cohesive or sticky materials that may have difficulty blending in other types of mixers. |
Gentle Mixing: The controlled shear and tumbling action of conical blenders are gentle on sensitive or fragile materials, reducing the risk of product degradation. |
Versatility: These blenders can handle a wide range of materials, including powders, granules, and even materials with a wide disparity in particle sizes. |
Ease of Cleaning: Many conical blenders are designed for easy cleaning and sanitation, making them suitable for industries with strict hygiene requirements, such as pharmaceuticals and food processing. |

Disadvantages of Conical Blenders: |
Higher Initial Cost: Conical blenders can be more expensive to purchase and install compared to some other types of mixers. |
Batch Process: They are typically used for batch processing, which may not be suitable for continuous production lines. |
Complex Design: The presence of the helical screw adds complexity to the blender’s design, which may require more maintenance over time. |
Limited for Liquid Addition: Adding liquids to the blending process can be more challenging with conical blenders compared to some other mixer types. |
Limited for High-Shear Mixing: Conical blenders may not be ideal for applications that require high-shear mixing or intense agitation. |
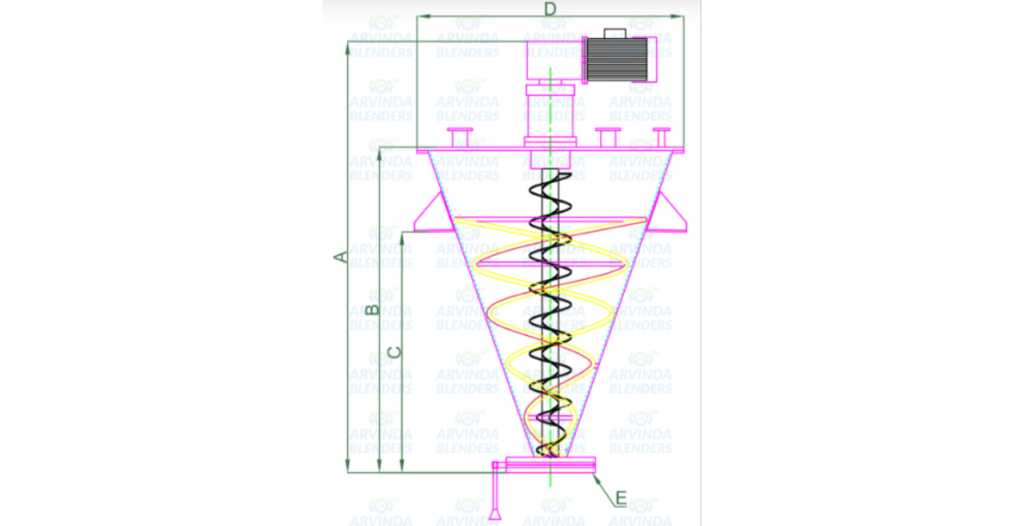
In summary, conical blenders are versatile and efficient mixing equipment suitable for a wide range of blending applications.
Their ability to handle cohesive materials and provide uniform mixing makes them valuable in industries where product quality and consistency are paramount. However, they may have a higher initial cost and require more maintenance compared to simpler mixing equipment.
The choice of blender type should be based on the specific needs and characteristics of the materials being blended.