HEAT EXCHANGERS
Heat Exchangers are mechanical devices or equipment designed for the efficient transfer of thermal energy (heat) between two or more fluids at different temperatures.
The primary purpose of a heat exchanger is to either heat a fluid or cool it, depending on the specific application.
Heat exchangers are widely used in various industrial processes, heating, ventilation, air conditioning (HVAC), and refrigeration systems, as well as in everyday appliances and systems.
The basic principle of a heat exchanger involves the transfer of heat from one fluid (often referred to as the “hot” or “primary” fluid) to another fluid (the “cold” or “secondary” fluid) without the two fluids coming into direct contact.
This separation is achieved by using a barrier or surface that allows heat to flow from one fluid to the other while preventing the fluids from mixing.
Heat exchangers can take various forms and configurations, depending on their intended use and design:
Shell and Tube Heat Exchangers: These consist of a bundle of tubes enclosed in a cylindrical shell. One fluid flows through the tubes, while the other flows through the shell, allowing for efficient heat transfer.
Plate Heat Exchangers: Plate heat exchangers consist of multiple thin metal plates with channels for fluid flow. These are compact and efficient for a wide range of applications.
Finned Tube Heat Exchangers: These heat exchangers have tubes with fins on the outside, which increase the surface area for heat transfer, making them efficient for air cooling or heating.
Double-Pipe Heat Exchangers: These have two concentric pipes or tubes, with one fluid flowing through the inner tube and the other through the annular space between the tubes.
Air-Cooled Heat Exchangers: Used to remove heat from processes by passing air over finned tubes or coils carrying the hot fluid.
Heat exchangers are employed in numerous applications, including:
- Heating and cooling of buildings and HVAC systems.
- Industrial processes, such as chemical manufacturing and power generation.
- Refrigeration and air conditioning systems.
- Oil and gas processing, including heat recovery.
- Food and beverage processing.
- Solar water heaters.
- Waste heat recovery.
- Automotive and engine cooling systems.
The efficiency and performance of a heat exchanger depend on factors like the design, materials of construction, flow rates, temperature differences, and the type of fluids being used. Heat exchangers play a crucial role in conserving energy, enhancing process efficiency, and maintaining desired temperatures in various systems.
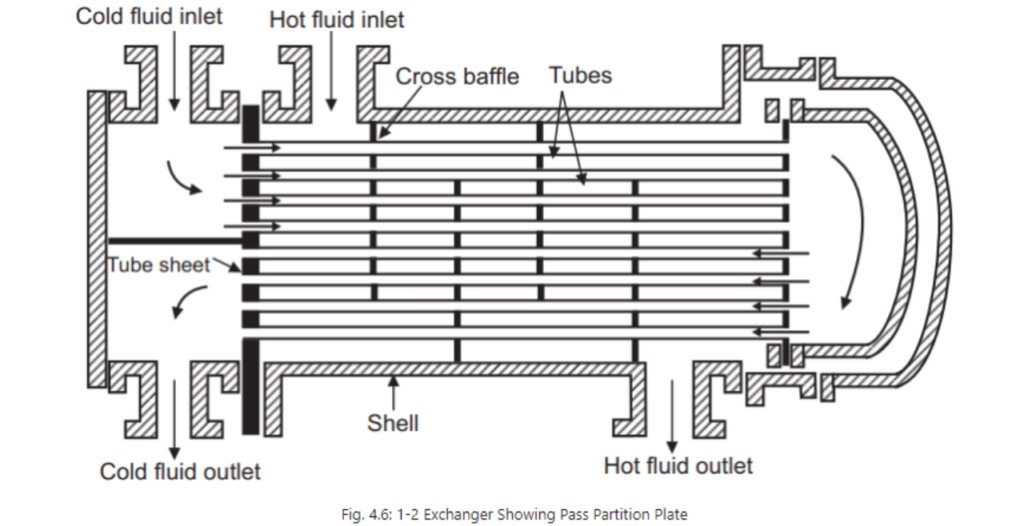
Heat exchangers serve several important purposes in various industrial and everyday applications.
Their primary function is to facilitate the efficient transfer of thermal energy (heat) between two or more fluids at different temperatures. The key purposes of heat exchangers are as follows:
Heating: Heat exchangers are commonly used to heat fluids. For instance, they play a vital role in heating water for residential and commercial applications, such as hot water systems, central heating, and industrial processes.
Cooling: Heat exchangers are employed for cooling purposes by transferring heat from a hot fluid to a cooler fluid. This is essential in air conditioning systems, refrigeration units, and engine cooling in vehicles.
Energy Recovery: Heat exchangers are used to recover waste heat from various industrial processes and systems. This recovered heat can be redirected for space heating, water heating, or to improve the overall energy efficiency of a facility.
Temperature Control: They help control the temperature of a fluid within a specified range, ensuring that it remains within the desired operational limits.
Process Heating and Cooling: In manufacturing and chemical processes, heat exchangers are integral for maintaining precise temperature control in various production steps, leading to product quality and consistency.
Heat Transfer and Heat Exchange: They are designed to enhance heat transfer and heat exchange between two fluids without mixing them. This is vital for applications like heat recovery in power plants and industrial facilities.
Efficiency Enhancement: Heat exchangers can improve the overall energy efficiency of systems, reducing energy consumption and operating costs.
Heat Removal: They are essential for removing excess heat generated during various processes, preventing overheating and potential equipment damage.
Condensation and Evaporation: Heat exchangers facilitate the condensation and evaporation of fluids, which are fundamental processes in refrigeration cycles and industrial applications.
Environmental Control: In environmental control systems, like flue gas desulfurization units in power plants, heat exchangers help control the temperature of gases and remove pollutants efficiently.
Heat Recovery and Recirculation: They enable the recovery of heat from exhaust gases or waste streams and can be used to preheat or heat incoming fluids in industrial processes.
Coolant Circulation: In vehicles, heat exchangers are critical for engine cooling, ensuring that the engine operates within a safe temperature range.
Chemical Processes: In chemical manufacturing, heat exchangers are used for various purposes, such as heating reactants, cooling exothermic reactions, and condensing volatile chemicals.
Refrigeration: They are essential components in refrigeration systems, where they help remove heat from the refrigerant and maintain low temperatures inside refrigerated spaces.
Solar Energy Systems: In solar water heaters and solar thermal systems, heat exchangers transfer heat from solar collectors to water or another heat transfer fluid.
Heat exchangers come in various types and designs to suit specific applications, and they play a crucial role in enhancing energy efficiency, product quality, and overall system performance in a wide range of industries and systems.
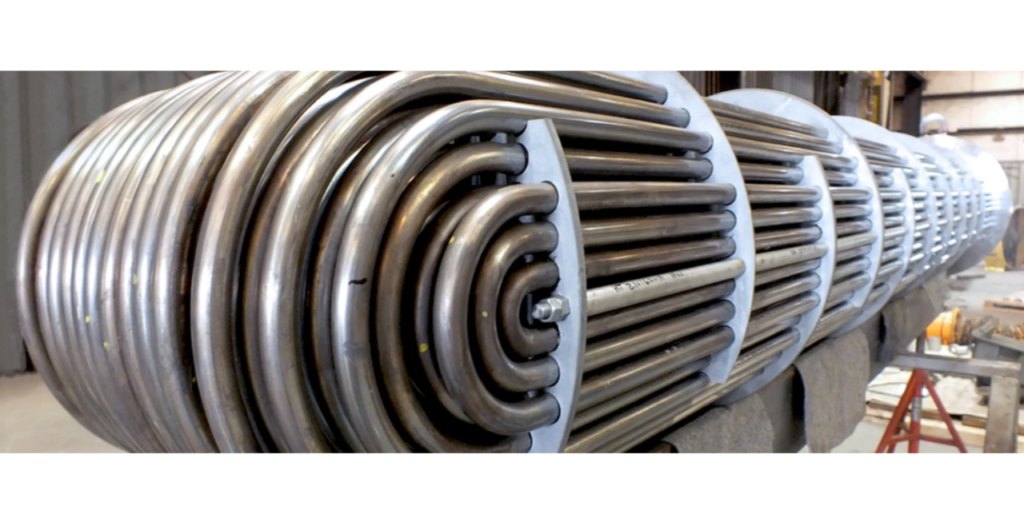

Designing a heat exchanger involves several steps and considerations to ensure efficient heat transfer while meeting the specific requirements of the application.
The design process can vary depending on the type of heat exchanger, the properties of the fluids involved, the desired heat transfer rate, and other factors. Here’s a general outline of how to design a heat exchanger:
Determine the Purpose and Specifications:
- Define the purpose of the heat exchanger (e.g., heating, cooling, heat recovery).
- Specify the required heat transfer rate (Q), temperature ranges, and flow rates of the hot and cold fluids.
- Identify any constraints or limitations, such as space, pressure, and material compatibility.
Select the Type of Heat Exchanger:
- Choose the appropriate type of heat exchanger based on the application, fluid properties, and efficiency requirements. Common types include shell and tube, plate, and finned tube heat exchangers.
Fluid Properties:
- Gather and analyze the properties of the fluids involved, including thermal conductivity, specific heat, density, and viscosity.
- Determine any changes in properties due to temperature variations.
Temperature Difference (ΔT):
- Calculate the required temperature difference between the hot and cold fluids for efficient heat transfer. This is often based on the specific heat capacities of the fluids and the desired heat transfer rate.
Heat Transfer Surface Area (A):
- Calculate the required heat transfer surface area using the formula: Q = U * A * ΔT, where U is the overall heat transfer coefficient.
- The overall heat transfer coefficient takes into account the thermal resistance of the heat exchanger materials and fouling factors.
Heat Exchanger Sizing:
- Determine the dimensions of the heat exchanger, including the length and diameter of tubes in a shell and tube heat exchanger or the number of plates in a plate heat exchanger.
- Consider the arrangement of tubes or plates to maximize heat transfer efficiency.
Flow Arrangement and Passes:
- Choose the flow arrangement for the hot and cold fluids (parallel, counterflow, or crossflow) based on the specific application and temperature requirements.
- Determine the number of flow passes through the heat exchanger to optimize heat transfer.
Material Selection:
- Select materials of construction for the heat exchanger based on fluid compatibility, corrosion resistance, and mechanical strength.
Pressure Drop:
- Calculate the pressure drop on both the hot and cold sides of the heat exchanger to ensure that the fluid flows at the desired rates.
Design Features:
- Consider additional design features, such as baffle spacing, fin types (if applicable), and tube layout for shell and tube heat exchangers.
Thermal and Mechanical Design:
- Perform thermal design calculations to ensure that the heat exchanger will meet the heat transfer requirements.
- Perform mechanical design calculations to ensure that the heat exchanger can withstand the operating pressures and stresses.
Safety and Regulation Compliance:
- Ensure that the heat exchanger design complies with safety standards, regulations, and industry codes.
Testing and Validation:
- Conduct tests or simulations to validate the design, taking into account factors like fouling, vibration, and heat exchanger performance under various conditions.
Documentation and Drawings:
- Prepare detailed engineering drawings and documentation for the construction and fabrication of the heat exchanger.
Fabrication and Installation:
- Fabricate the heat exchanger using the specified materials and design details, and install it according to the project requirements.
The design of heat exchangers is a complex process that requires a thorough understanding of fluid mechanics, thermodynamics, and materials science.
Consulting with experts in heat exchanger design and analysis is often necessary to ensure the design meets performance, efficiency, and safety objectives.
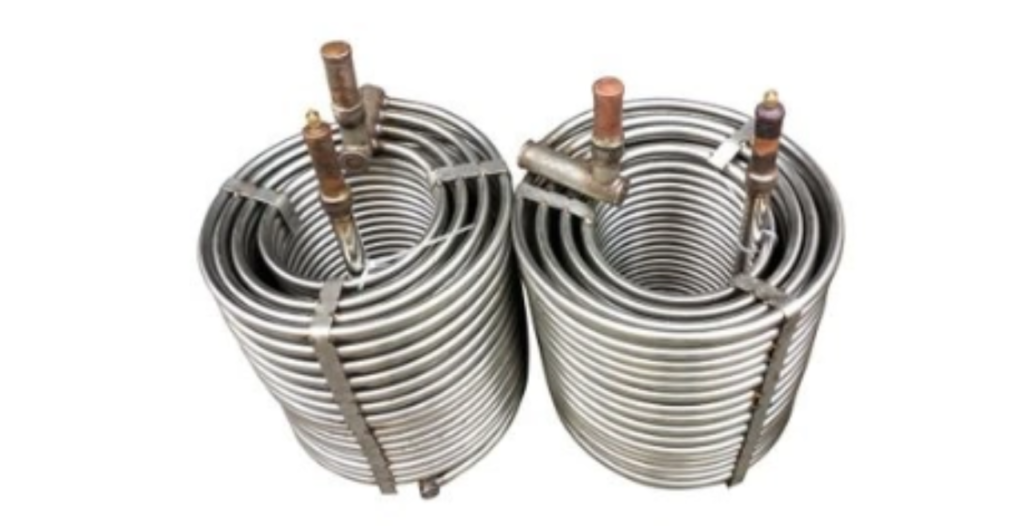

Heat exchangers are integral to modern industrial processes, environmental control, and everyday comfort systems, playing a key role in energy conservation and the efficient use of resources.
Their design and operation are essential for achieving specific temperature and heat transfer requirements in a wide range of applications.
If you have specific inquiries about any type of Heat Exchangers or require design services, please contact our Sales Team @ T.E.A.M. Engineer’s Multi-Equipment & Multi-Services Pvt. Ltd. as soon as possible.