T.E.A.M.'s Candle Filters:
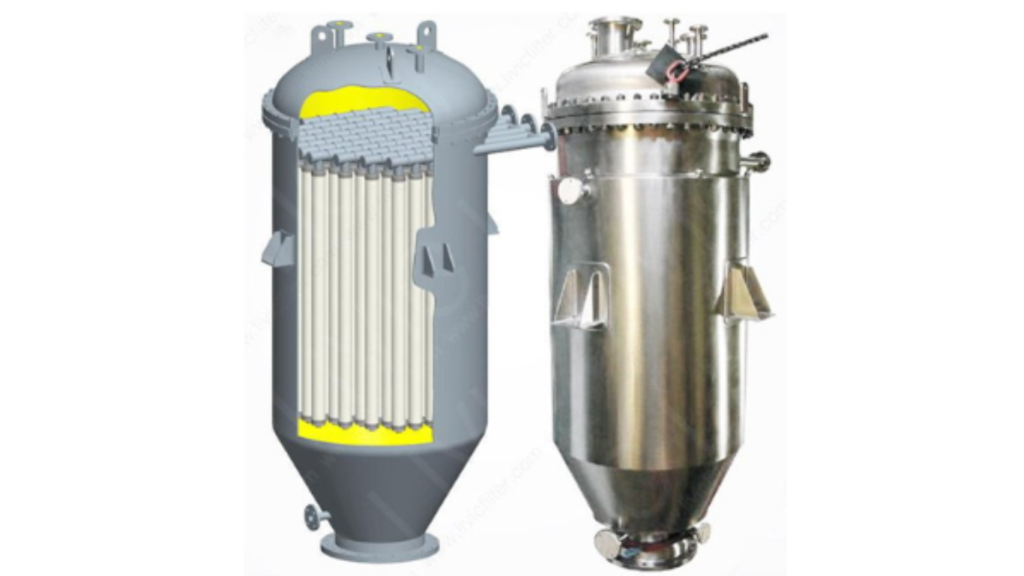
Candle Filter: In the context of process equipment manufacturing, a “candle filter” refers to a specific type of filtration system especially used in industries such as chemical processing, pharmaceuticals, food and beverage.
candle filter is nothing but a pressure-type filter used in process equipment manufacturing and typically consists of a cylindrical housing with multiple vertical filter elements, resembling candles, enclosed within it.
These filter elements are usually made of different types of materials such as pp, MS, CS, SS304, SS304L, SS316, SS316L, or based on custom-built requirements. Each candle filter element contains a large surface area designed to trap and retain solid particles while allowing the desired fluid to pass through.
The working principle of a candle filter involves directing the fluid to be filtered into the housing and through the filter elements. The solid particles or contaminants present in the fluid are captured by the filter media, while the clarified fluid flows out of the system.
Candle filters in process equipment manufacturing are known for their ability to handle high flow rates and provide efficient separation of solids from liquids. They are often used for tasks such as removing fine particles, catalyst recovery, product purification & clarification of liquids.
Candle filters offer advantages such as high filtration efficiency, long service life and easy maintenance. Depending on the application, the filter elements may be cleaned periodically through backwashing or regenerative techniques, or they may be replaced when they become saturated with contaminants.
For removal of the cake, compressed air/nitrogen or any compatible liquid is given in the reverse direction.
Overall, Candle Filters are widely used in process equipment manufacturing as a reliable and effective filtration solution for solid-liquid separation, offering high performance and versatility in diverse industrial settings.
Benefits:
- Higher cake holding capacity if compared with other pressure filters.
- Clean surroundings area clean in place filtration.
- No operator exposure to filtration fluid/cake.
- No emission of filtration fluids into the atmosphere.
- Less product loss in cake due to higher dryness.
- Minimum downtime of the filter due to backwashing.
- Longer life of the filter element due to in situ cleaning
- Complete automation possible
- Quick payback period
Silent Features:
- Filtration in closed condition.
- Cake discharge in closed condition.
- Least heel volume
- Suitable for both direct filtrations.
- Suitable for pre-coat filtrations
- Excellent regeneration of the filtration area after backwashing.
- Cake removal either by blowback or backwashing
- Highest cake stability due to the unique shape of the candles
- Easier cake removal due to surface filtration
Materials of Constructions (MOC):
- MS
- CS
- SS304
- SS304L
- SS316
- SS316L
- Candles in PP, SS316L, SS316, SS304, SS304L, MS & CS
Applications:
- Removal of activated carbon
- Sugar solutions
- Recovery of catalysts
- Chemicals
- Removal of bleaching earth
- Textile
- Solvents
- Recovery of metals & Metallic oxides
- Bulk drug solutions
- Filtration of Urea solution
- Paints & Pigments
- Oil & Gas industries
- Filtration of glycerine water
- Lubricating oils