DRYERS TECHNOLOGY & PRODUCTS
Spray Dryers
Spray dryers are widely used in process industries for converting liquid or slurry feedstocks into dry powders or granules.
They are versatile drying systems that use a combination of atomization, hot air, and rapid evaporation to remove moisture from materials. Spray dryers are employed in various industries, including food, pharmaceuticals, chemicals, and ceramics.
Here’s more information about spray dryers, including their working principles, advantages, disadvantages, applications, materials of construction (MOC), and a summary:
Working Principles: The working principles of spray dryers involve several key steps:
Atomization: The feedstock, which is usually in liquid or slurry form, is pumped into the top of the dryer and atomized into tiny droplets using a high-pressure nozzle or rotary atomizer.
Contact with Hot Air: Hot air, preheated to the desired temperature, is introduced into the drying chamber. The atomized droplets are immediately exposed to the hot air.
Evaporation: As the atomized droplets contact the hot air, rapid evaporation occurs. Moisture is removed from the droplets, leaving behind dry particles.
Separation: The dry particles are separated from the hot air using a cyclone separator, bag filter, or other collection system. The dried product is collected, while the hot air is recirculated or discharged.

Advantages:
Rapid Drying: Spray dryers can achieve rapid moisture removal due to the large surface area of atomized droplets exposed to hot air.
Controlled Process: Operators can control temperature, feed rate, and airflow to achieve precise drying results.
Uniform Drying: Spray dryers produce uniform and consistent particles, which is essential for product quality.
Wide Range of Applications: They are suitable for various materials, including heat-sensitive products, chemicals, dairy products, and pharmaceuticals.
Product Formulation: Spray drying allows for the formulation of products with specific particle sizes and characteristics.
Disadvantages:
High Initial Cost: The equipment and installation costs of spray dryers can be relatively high.
Maintenance: Maintenance requirements can be significant, especially for larger and more complex systems.
Energy Consumption: Operating spray dryers at high temperatures can result in relatively high energy consumption.

Applications: Spray dryers are used in numerous industries and applications, including:
- Food Industry: Drying food products like milk and coffee extracts, flavors, and starches.
- Pharmaceuticals: Drying pharmaceutical powders, granules, and active ingredients.
- Chemical Processing: Drying chemicals, pigments, and catalysts.
- Ceramics: Producing ceramic powders for use in ceramics manufacturing.
- Environmental Remediation: Drying and processing waste materials.
- Detergents and Soaps: Drying detergent powders and granules.
Materials of Construction (MOC): The choice of materials for spray dryers depends on factors such as the specific application, material being processed, and potential corrosive or abrasive properties. Common materials of construction include:
- Stainless Steel: Used for its corrosion resistance and cleanliness in food and pharmaceutical applications.
- Carbon Steel: Suitable for many industrial applications.
- Specialized Alloys: Used in high-temperature or corrosive environments.
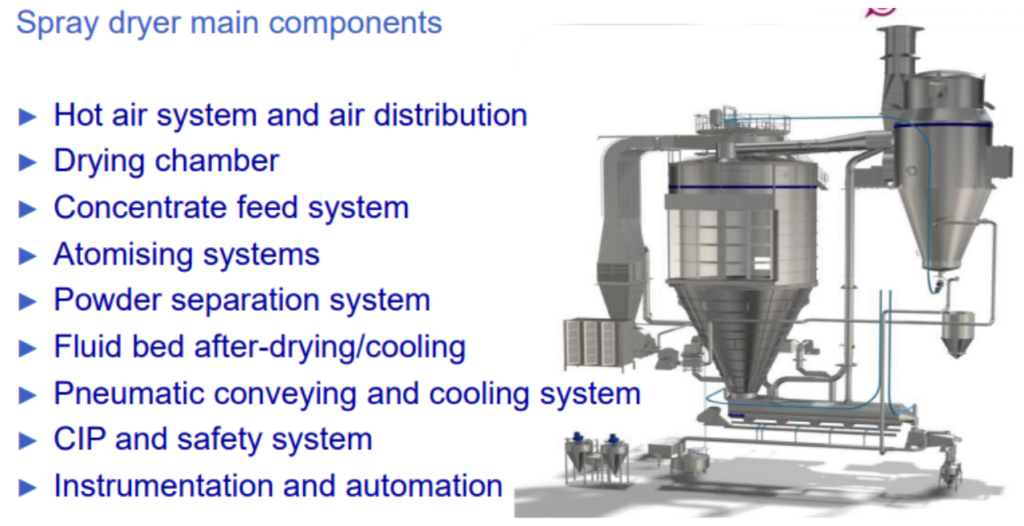
Summary: Spray dryers are versatile industrial drying systems that efficiently convert liquid or slurry feedstocks into dry powders or granules. They operate based on atomization, rapid evaporation, and controlled temperature and airflow. While they offer rapid drying, precise control, and uniform product quality, they can be expensive to purchase and maintain. Spray dryers find applications in diverse industries, including food, pharmaceuticals, chemicals, and ceramics, and their materials of construction are chosen based on the specific requirements of the application.