Evaporation Technology/Products
Falling Film Evaporator
Falling Film Evaporator (FFE) is a widely used piece of equipment in evaporation technology for concentrating liquid solutions, particularly those with heat-sensitive components or those that require precise control over concentration levels.
FFEs are commonly used in various industries, including the food, pharmaceutical, and chemical sectors. Here’s an overview of their working principles, advantages, and disadvantages

Working Principle: The working principle of a Falling Film Evaporator involves several key steps:
Feed Introduction: The liquid solution to be concentrated is introduced into the FFE through a distribution system.
Formation of Falling Film: The feed is evenly distributed to the top of vertical heat exchanger tubes or plates within the FFE. These tubes or plates are heated by steam or another heating medium. As the liquid flows downward under gravity, it forms a thin film on the inner surfaces of the heat exchanger.
Heat Transfer: The heating medium inside the tubes or plates transfers heat to the liquid film. This causes the solvent within the liquid to evaporate, leaving behind the concentrated product.
Vapor Generation: The vapor generated during the evaporation process rises to the top of the FFE and is typically collected and condensed for further use or disposal.
Concentration: As the liquid film descends along the heat exchanger, it becomes progressively more concentrated, reaching the desired concentration level at the bottom of the unit.
Product Discharge: The concentrated product is continuously removed from the bottom of the FFE.
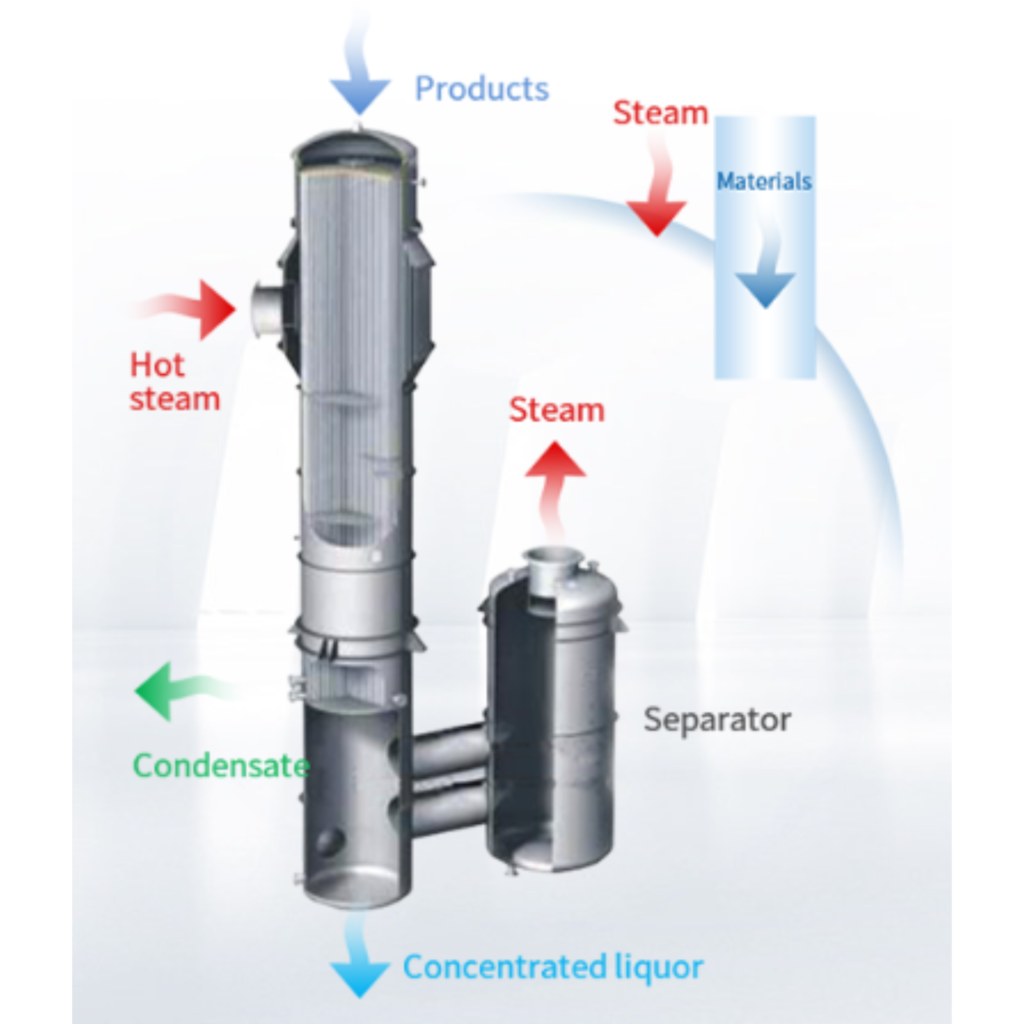

Advantages of Falling Film Evaporators:
Gentle Processing: FFEs are well-suited for heat-sensitive materials since they operate at relatively low temperatures under vacuum, reducing the risk of product degradation.
High Efficiency: The thin film formation and high heat transfer surface area result in efficient evaporation and concentration.
Continuous Operation: Falling Film Evaporators are often designed for continuous processing, making them suitable for industrial-scale operations.
Reduced Fouling: The falling film configuration minimizes fouling and scaling on the heating surfaces, improving operational efficiency and reducing maintenance needs.
Precise Control: FFEs offer precise control over the concentration of the final product, making them suitable for applications requiring specific concentration levels.
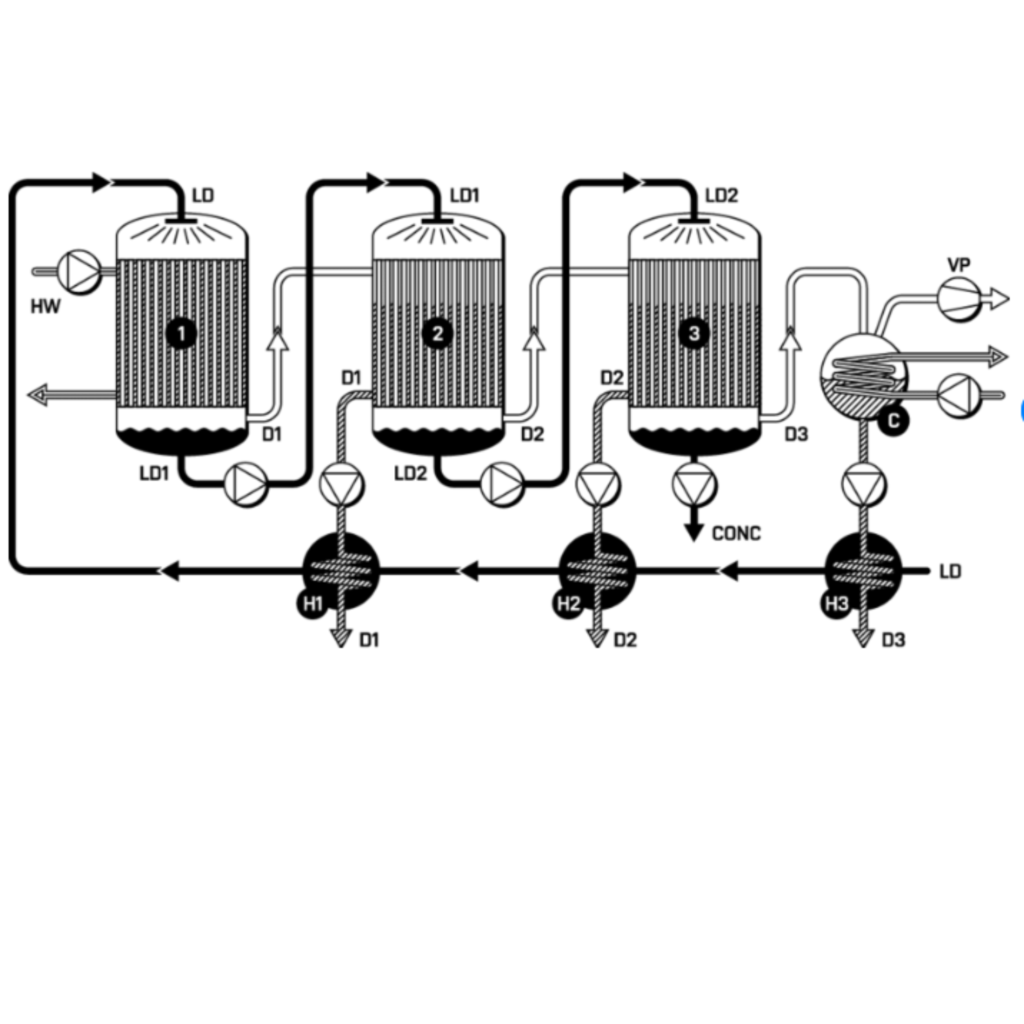
Disadvantages of Falling Film Evaporators:
Initial Cost: The equipment cost for FFEs can be relatively high compared to simpler evaporators.
Not Suitable for Viscous Liquids: FFEs may not be as effective for liquids with very high viscosity, as they may not form a uniform falling film.
Limited for Solids Handling: While suitable for some applications, FFEs may not be the best choice for processing materials with a high solid content.
Complex Design: FFEs can have a complex design with heat exchanger tubes or plates, which may require more maintenance and cleaning.
Energy Consumption: Operating FFEs may require significant energy input, especially for the heating and vacuum systems.

In summary, Falling Film Evaporators are efficient and versatile pieces of equipment used for concentrating liquid solutions, particularly those that are heat-sensitive or require precise concentration control. Their ability to operate continuously and their gentle processing make them valuable in various industrial applications. However, their initial cost and complexity should be considered when selecting them for a specific application.