Automated Weighing and Batching System
From: BULK SOLID CONVEYING & GRAIN HANDLING SYSTEMS
Automated Weighing and Batching System is integral components in processing industries, used to precisely measure and mix various materials in a controlled and automated manner. These systems play a crucial role in ensuring product quality, consistency, and efficiency in industries such as food and beverage, pharmaceuticals, chemicals, and construction materials. In this detailed overview, we will discuss the key aspects of automated weighing and batching systems, including equipment, working principles, advantages, disadvantages, applications, materials of construction (MOC), and provide a summary. |
1. Working Principles: Automated weighing and batching system use a combination of sensors, controllers, conveyors, and precision measuring equipment to accurately weigh and combine materials. The key working principles include: |
Material Flow Control: The system controls the flow of various materials from storage silos, bins, or bags using conveyors, augers, or pneumatic systems. |
Weighing and Measurement: Materials are weighed using load cells or other weighing technology with high precision. |
Recipe Management: The system utilizes recipes or formulas to specify the quantity and order of materials to be combined. |
Automation and Control: Programmable logic controllers (PLCs) or computerized control systems automate the process, ensuring accurate weighing and batching according to the recipe. |
2. Equipment: Automated weighing and batching system consist of several essential components: |
Material Feeders: These devices, such as belt conveyors, screw feeders, and vibratory feeders, transport materials from storage to the weighing process. |
Weighing Equipment: Load cells, scales, or other precision measuring devices are used to accurately measure the weight of materials. |
Control Systems: PLCs, computers, or dedicated control panels manage the process, including recipe selection, material flow control, and data logging. |
Mixing Equipment: In some applications, mixers or blenders are integrated to homogenize the batch. |

3. Advantages: |
Precise control over material quantities, ensuring product consistency. |
Enhanced production efficiency and reduced material wastage. |
Reduced labor costs and improved worker safety. |
Accurate tracking and reporting for quality control and regulatory compliance. |
Suitable for a wide range of industries and materials. |
4. Disadvantages: |
High initial setup and equipment costs. |
Maintenance and calibration requirements to ensure accuracy. |
Complexity in system design and integration. |
Risk of system downtime in case of malfunctions. |
Limited flexibility for rapid recipe changes. |

5. Applications: Automated weighing and batching system find applications in numerous industries, including: |
Food and Beverage: Mixing ingredients for baking, brewing, and food production. |
Pharmaceuticals: Precise blending of active pharmaceutical ingredients (APIs) for drug manufacturing. |
Chemicals: Accurate dosing of chemicals for chemical processing and manufacturing. |
Construction Materials: Producing concrete, asphalt, and other building materials. |
Agriculture: Mixing fertilizers and animal feed ingredients. |
6. Materials of Construction (MOC): The choice of materials for construction depends on the specific application and industry requirements: |
Stainless Steel: commonly used for parts that come into contact with food, pharmaceuticals, or corrosive materials. |
Carbon Steel: Suitable for non-corrosive industrial applications. |
Plastics: Used for components in non-food and non-pharmaceutical applications. |
Coatings: Some parts may have specialized coatings to enhance durability and corrosion resistance. |
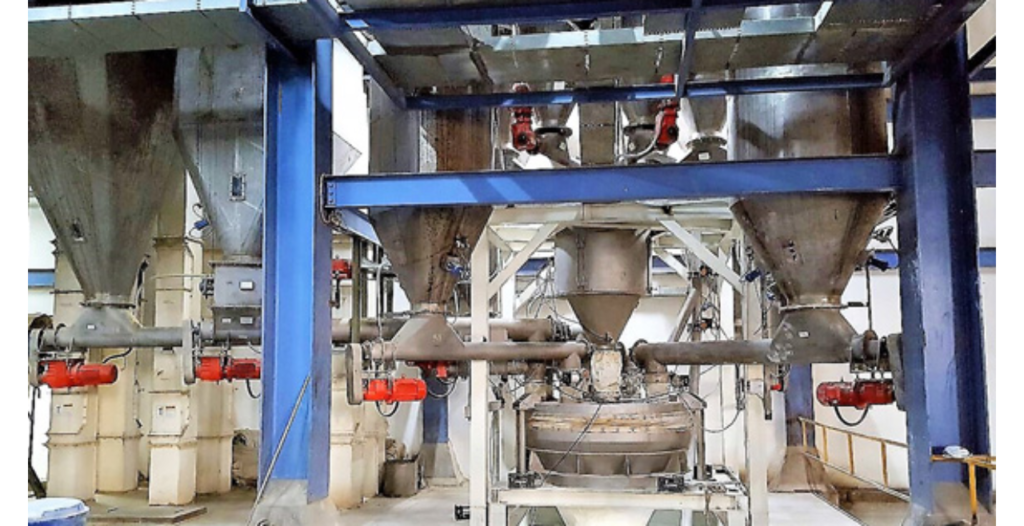
7. Summary:
Automated weighing and batching system is crucial in processing industries for precise measurement and mixing of materials.
They rely on advanced control systems, conveyors, and weighing equipment to ensure accurate and consistent batching according to predefined recipes.
These systems offer advantages such as improved product quality, efficiency, and labor savings but come with initial setup costs, maintenance requirements, and complexities in design and integration.
They find applications in food and beverage, pharmaceuticals, chemicals, construction materials, and agriculture, with the choice of materials tailored to industry-specific needs.