DRYERS TECHNOLOGY & PRODUCTS
Rotary Dryers
Rotary dryers are industrial drying systems used in various process industries to remove moisture or water content from bulk materials, such as minerals, chemicals, food products, and agricultural products. Here’s more information about rotary dryers in process industries, including their working principles, advantages, disadvantages, applications, materials of construction (MOC), and a summary: |
Working Principles: The working principles of rotary dryers involve several key steps: |
Loading: The wet or moist material is loaded into a rotating drum or cylinder. |
Heating: Heat is applied to the exterior of the drum, typically using combustion gases, hot air, or steam. The heat source can be direct or indirect, depending on the application. |
Tumbling: As the drum rotates, the material inside tumbles and is exposed to the heated surface. This exposes a large surface area of the material to the drying medium, facilitating the evaporation of moisture. |
Moisture Evaporation: Moisture within the material vaporizes and turns into steam due to the heat. The moisture-laden air is then removed from the drum. |
Discharge: The dried material is discharged from the drum once it reaches the desired moisture content. |
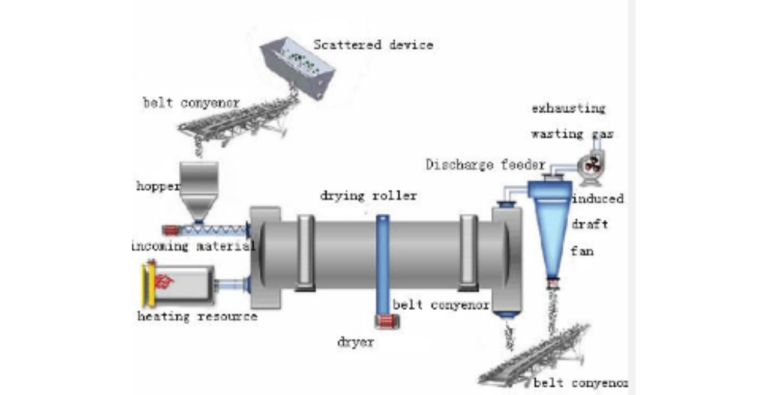
Advantages: |
High Capacity: Rotary dryers can handle large quantities of material, making them suitable for industrial-scale drying operations. |
Uniform Drying: The tumbling action ensures uniform drying of the material, reducing the risk of over-drying or under-drying. |
Versatility: Rotary dryers can be adapted for various materials and moisture content ranges. |
Energy Efficiency: Modern designs often include heat recovery systems, improving energy efficiency. |
Continuous Operation: They allow for continuous and automated drying processes, reducing labor requirements. |
Disadvantages: |
Complexity: Rotary dryers can be complex to operate and maintain, requiring specialized knowledge. |
Initial Cost: The equipment and installation costs can be relatively high. |
Material Handling: Some materials may require special handling to prevent agglomeration or sticking to the drum. |
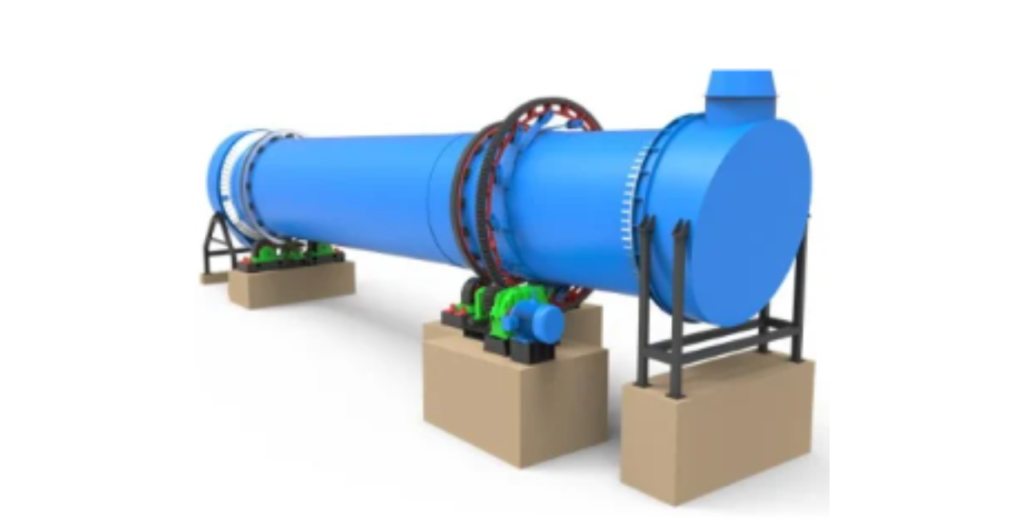
Applications: Rotary dryers find applications in numerous process industries, including: |
Mineral Processing: Drying ores, concentrates, and minerals before further processing. |
Chemical Processing: Drying chemicals, fertilizers, and pharmaceutical products. |
Food Industry: Drying fruits, vegetables, grains, and food ingredients. |
Agriculture: Drying crops like rice, grains, and seeds. |
Environmental Remediation: Drying sludges and waste materials. |
Biomass and Bioenergy: Drying biomass materials for use in bioenergy production. |

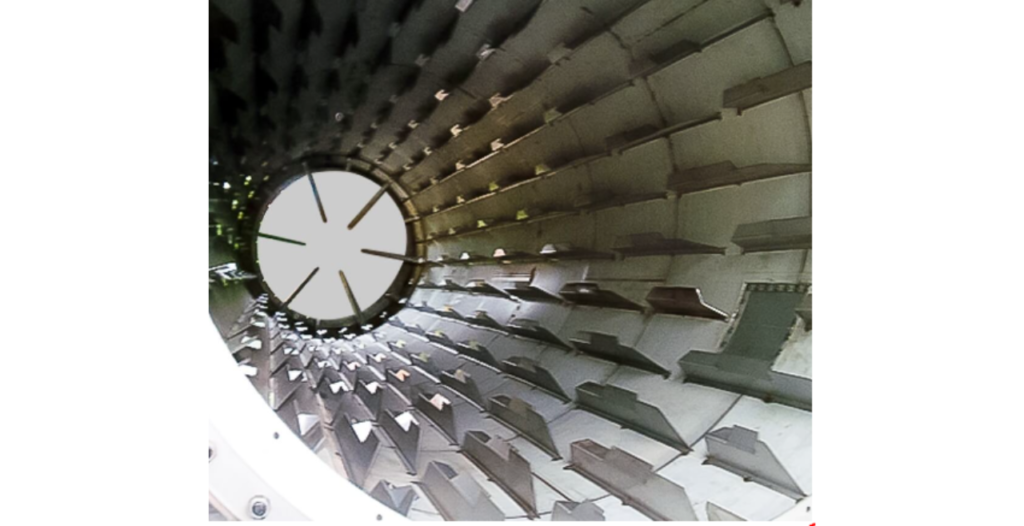
Materials of Construction (MOC): The choice of materials for rotary dryers depends on the specific application, but common materials used include: |
Carbon Steel: Suitable for many applications. |
Stainless Steel: Used when corrosion resistance is needed. |
Specialized Alloys: Used in high-temperature or corrosive environments. |
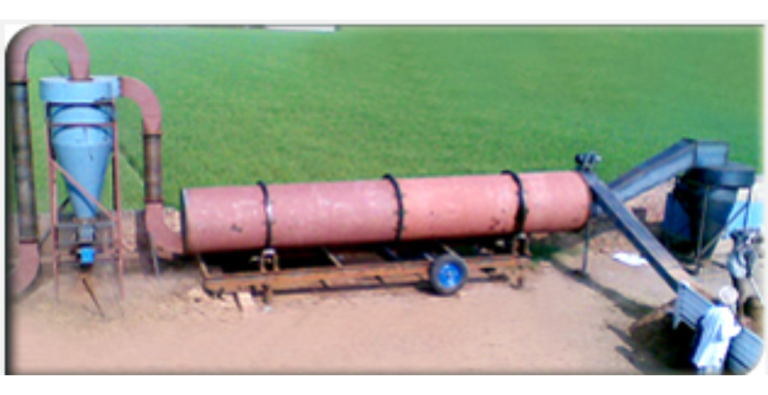
Summary: Rotary dryers are essential equipment in process industries for removing moisture from bulk materials efficiently and uniformly. They operate by heating the material within a rotating drum, allowing moisture to evaporate and be removed. Rotary dryers are favored for their high capacity, uniform drying, versatility, and energy efficiency. However, they can be complex to operate and have an initial cost associated with their installation. They find wide-ranging applications in industries such as mining, chemicals, food processing, agriculture, and more, and their materials of construction are selected based on the specific requirements of the application. |
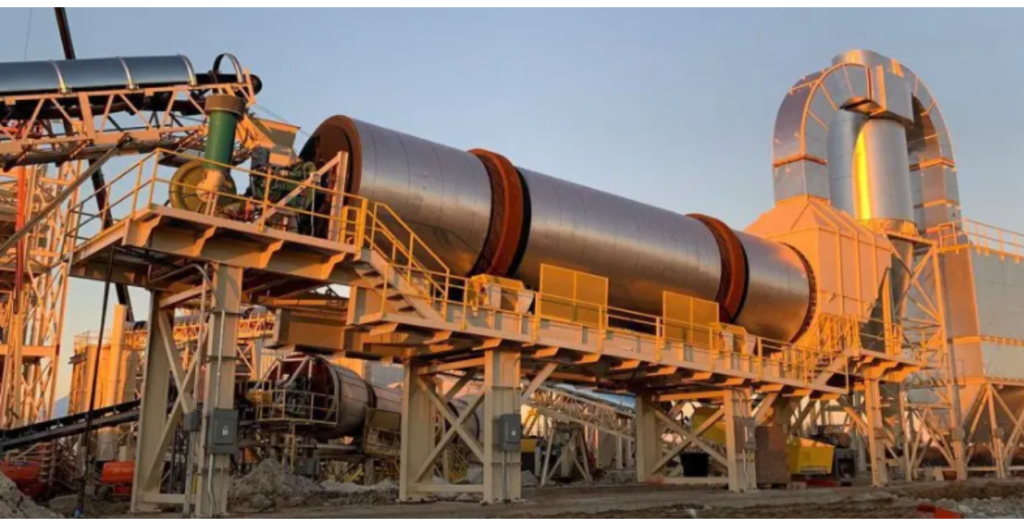
The rotary dryer is a type of industrial dryer employed to reduce or minimize the liquid moisture content of the material it is handling by bringing it into direct contact with a heated gas. The dryer is made up of a large, rotating cylindrical tube, usually supported by concrete columns or steel beams. The dryer slopes slightly so that the discharge end is lower than the material feed end in order to convey the material through the dryer under gravity. Material to be dried enters the dryer, and as the dryer rotates, the material is lifted up by a series of internal fins lining the inner wall of the dryer. When the material gets high enough to roll back off the fins, it falls back down to the bottom of the dryer, passing through the hot gas stream as it falls. This gas stream can either be moving toward the discharge end from the feed end (known as co-current flow), or toward the feed end from the discharge end (known as counter-current flow). The gas stream can be made up of a mixture of air and combustion gases from a burner, in which case the dryer is called a direct heated dryer. Alternatively, the gas stream may consist of air or another (sometimes inert) gas that is preheated. When the gas stream is preheated by some means where burner combustion gases do not enter the dryer, the dryer known as an indirect-heated type. Often, indirect heated dryers are used when product contamination is a concern. In some cases, a combination of direct-indirect heated rotary dryers are also available to improve the overall efficiency. |