AIR POLLUTION CONTROL SYSTEMS
Bag Filtration Systems
Bag Filtration Systems are widely used in processing industries to efficiently remove dust, particulate matter, and pollutants from gas streams. These systems are essential for maintaining clean air quality, protecting equipment, and ensuring compliance with environmental regulations. In this detailed overview, we will discuss the key aspects of bag filtration systems, including equipment, working principles, advantages, disadvantages, applications, materials of construction (MOC), and provide a summary. |
1. Working Principles: Bag filtration systems operate on the principles of filtration and separation, using specially designed fabric or synthetic bags to capture and remove particles from gas streams. The key working principles include: |
Capture: Polluted gas flows through a network of filter bags. The particles are captured on the surface of the bags due to various mechanisms, including interception, diffusion, and impaction. |
Filtration: As gas passes through the filter media, particles are separated from the gas phase. The filter bags act as barriers, allowing clean air to pass through while retaining the particles. |
Cleaning: Over time, dust accumulates on the bag surface, causing pressure drop and reduced filtration efficiency. To maintain performance, bag filtration systems use cleaning mechanisms such as reverse air, pulse-jet cleaning, or shaker mechanisms to dislodge and remove the collected dust. |
Collection: The dust dislodged from the bags is collected in hoppers or other storage devices for disposal or recycling. |
2. Equipment: Bag filtration systems consist of several essential components and technologies: |
Filter Bags: These are the heart of the system, typically made of materials like polyester, polypropylene, PTFE, or fiberglass. The choice depends on the application and the properties of the dust being collected. |
Housing or Baghouse: The filter bags are housed in a structure designed to maintain airflow and create a controlled environment for efficient filtration. |
Cleaning Mechanisms: Systems may employ reverse air, pulse-jet cleaning, or shaker mechanisms to clean the filter bags. |
Hoppers and Discharge Devices: Dust collected in the baghouse is collected in hoppers and can be discharged for disposal or recycling. |

3. Advantages: |
High Efficiency: Bag filtration systems can achieve high removal efficiencies for particles of various sizes. |
Versatility: Suitable for a wide range of applications, from fine dust to larger particulate matter. |
Long Service Life: Properly maintained filter bags can have a long operational life. |
Compliance: Helps industries meet air quality regulations and emissions standards. |
Cost-Efficient: Operating costs are often lower compared to other air pollution control technologies. |
4. Disadvantages: |
Maintenance: Regular maintenance is required to replace filter bags, and cleaning mechanisms may require attention. |
Space and Installation: Baghouses can be large and require adequate space for installation. |
Energy Consumption: Energy is needed for fan operation and cleaning processes. |
Limited Use for Wet Particles: Bag filtration is not suitable for filtering wet or sticky materials. |
Temperature Limits: Bag materials may have temperature limitations. |
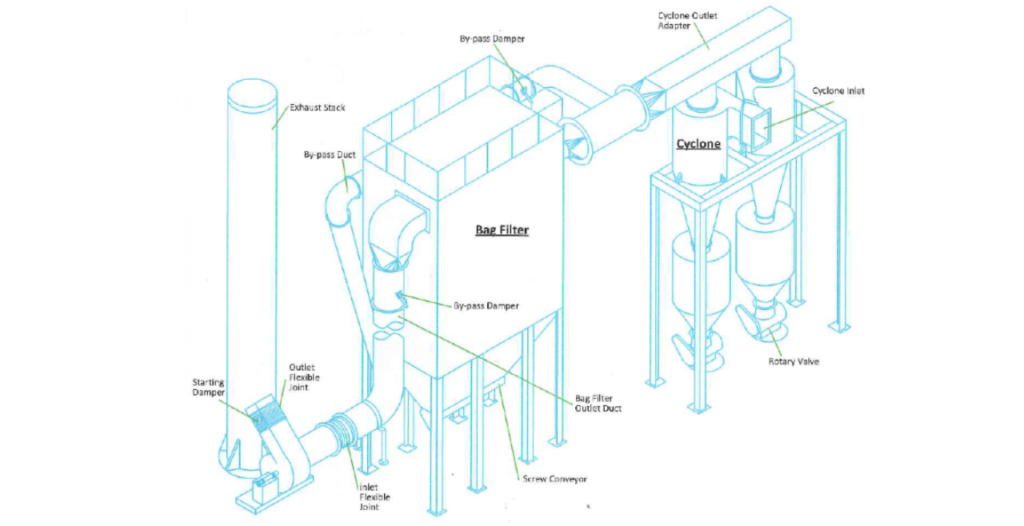
5. Applications: Bag filtration systems are widely used in various industries to control emissions and maintain air quality, including: |
Metalworking: Capturing particulate matter from welding, cutting, and grinding operations. |
Cement and Minerals: Reducing dust emissions from cement kilns and mining processes. |
Woodworking: Collecting wood dust in sawmills and woodworking shops. |
Food and Beverage: Capturing flour, sugar, and food ingredient dust in processing facilities. |
Pharmaceuticals: Controlling dust generated during drug manufacturing processes. |
Power Plants: Removing fly ash and other particulates from flue gas emissions. |
6. Materials of Construction (MOC): The choice of materials for bag filtration systems depends on factors such as the type of dust, temperature, and chemical compatibility. Common MOCs include: |
Polyester: Suitable for general industrial applications. |
Polypropylene: Resistant to moisture and some chemicals. |
PTFE (Polytetrafluoroethylene): Resistant to high temperatures and aggressive chemicals. |
Fiberglass: Suitable for high-temperature applications. |
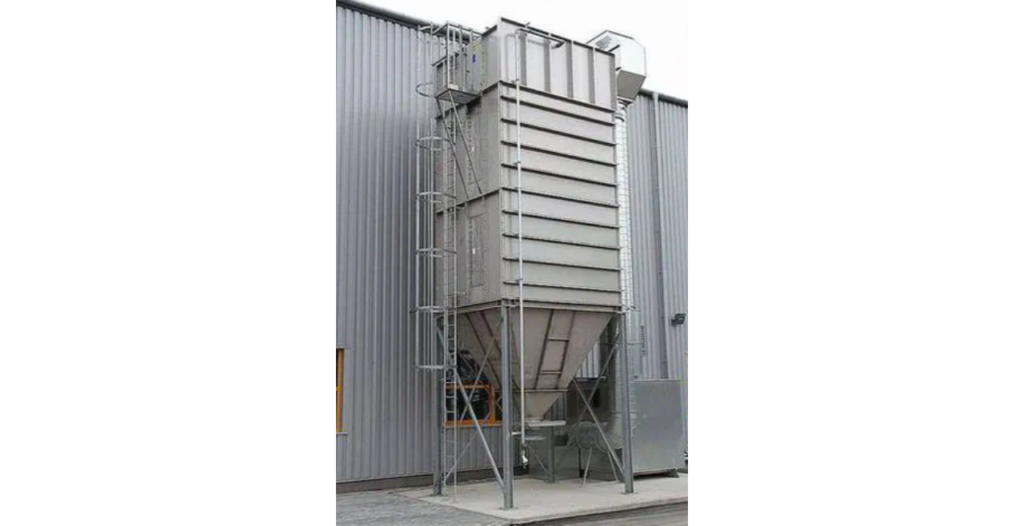
7. Summary: Bag filtration systems are essential components in processing industries for efficient removal of dust and particulate matter from gas streams.
They operate on principles of filtration, separation, cleaning, and collection. These systems offer advantages such as high efficiency, versatility, and compliance with environmental regulations. However, they require regular maintenance, adequate space for installation, and energy consumption.
Bag filtration finds applications in a wide range of industries, with the choice of materials of construction tailored to specific needs and environmental conditions.