Mixers/Blenders Technology/Products
High Shear Mixers:
High shear mixers are specialized mixing devices used in blending and mixing technology to thoroughly and efficiently homogenize a wide range of materials, including liquids, powders, granules, and other solid particles. They are known for their ability to achieve fine particle size reduction, dispersion, and emulsification. Here’s an overview of their working principles, advantages, and disadvantages:

High shear mixer operates on the principle of intense mechanical forces applied to the materials being mixed. The key working principles include: |
Rotor-Stator Configuration: High shear mixers typically consist of a rotor and stator configuration. The rotor, often in the form of a high-speed impeller or blade, rotates at high speed within a stationary stator. The close proximity and high-speed rotation of the rotor and stator generate intense shear forces in the mixing zone. |
Material Interaction: When the materials are introduced into the mixing chamber, they are subjected to the shear forces created by the rotor-stator configuration. This leads to several important mixing mechanisms: |
Shear: The high-speed rotation of the rotor generates shear forces that cause materials to flow past each other at different velocities, promoting mixing and particle size reduction. |
Cavitation: The rapid movement of the rotor can create localized low-pressure areas that lead to cavitation, which further enhances mixing and dispersion. |
Turbulence: The high shear rates result in turbulent flow within the mixing chamber, further promoting the breakup of particles and the incorporation of liquids into solids. |
Mixing Intensity: The intensity of mixing in high shear mixers can be adjusted by varying the rotor speed, the gap between the rotor and stator, and the design of the rotor and stator elements. |

Advantages of High Shear Mixers: |
Uniform Mixing: High shear mixers provide exceptional mixing uniformity, ensuring that all components are evenly distributed throughout the mixture. |
Particle Size Reduction: They are highly effective at reducing particle sizes, making them suitable for applications where fine particle size control is essential. |
Dispersion and Emulsification: High shear mixers excel at dispersing immiscible liquids and creating stable emulsions, making them valuable in industries like food processing, cosmetics, and pharmaceuticals. |
Rapid Mixing: They offer fast and efficient mixing, reducing processing times and improving production efficiency. |
Versatility: High shear mixers can handle a wide range of materials, from liquids and powders to highly viscous substances. |
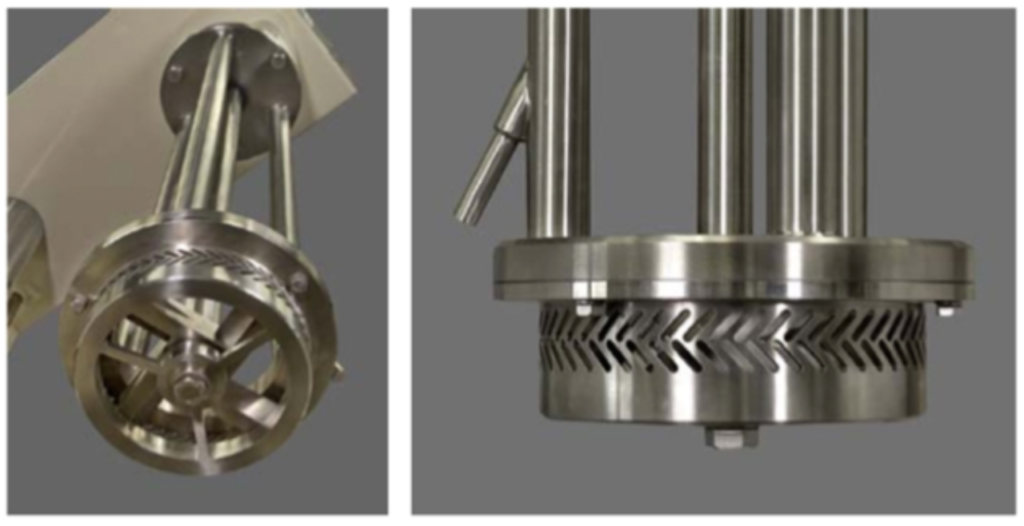
Disadvantages of High Shear Mixers: |
Energy Consumption: Achieving the intense shear forces in high shear mixers requires significant energy input, which can result in higher operating costs. |
Equipment Complexity: High shear mixers can be complex machines with numerous moving parts, which may require regular maintenance and replacement of wear components. |
Heat Generation: The intense mixing action can generate heat, which may be undesirable for temperature-sensitive materials. |
Limited for Large-Scale Production: While high shear mixers are suitable for lab-scale and small-scale production, they may not be as practical for very large-scale industrial processes. |
Cohesive Materials: Highly cohesive or adhesive materials may pose challenges in high shear mixers, potentially causing buildup on the rotor and stator. |

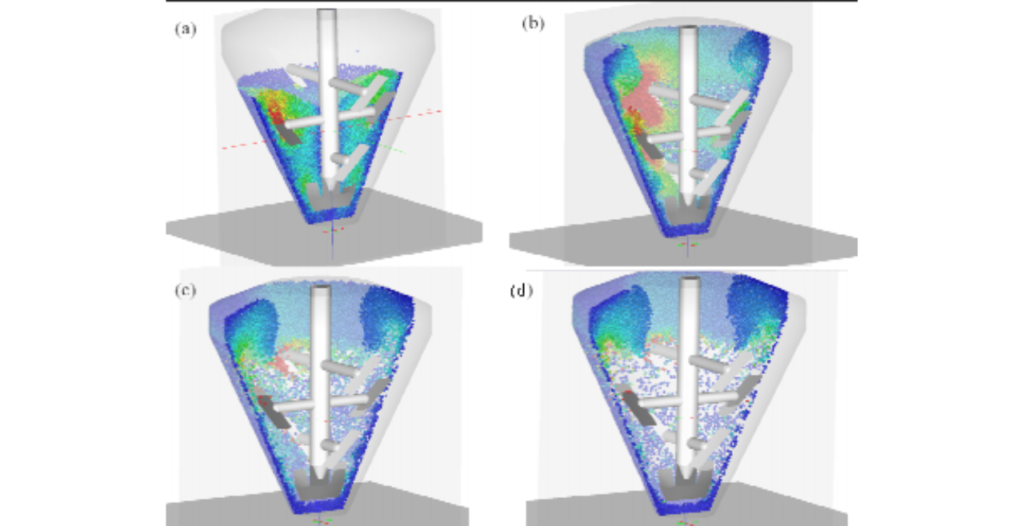

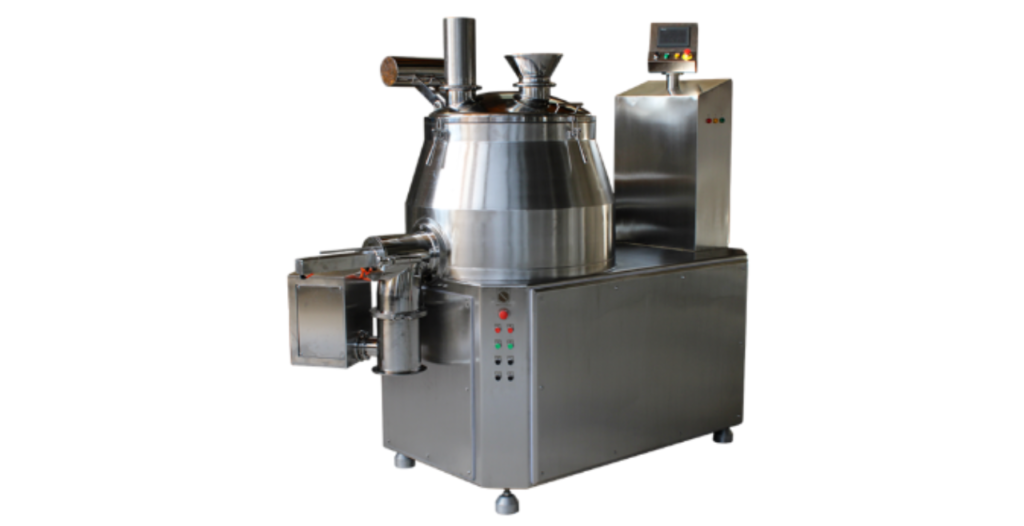
In summary, high shear mixers are versatile and powerful mixing devices widely used in various industries for achieving uniform mixing, particle size