GRINDING/MILLING/PARTICLE SIZE REDUCTION TECHNOLOGY & PRODUCTS
Flake Crusher Mill
Flake Crusher Mill / Breaker / Granulator Is a type of size reduction equipment used to crush & granulate Materials into Smaller & Manageable Flakes. |
Working Principles: |
The working principle of a Flake Crusher Mill involves the following steps: |
Feeding: The material is introduced into the crusher through a hopper or a feeding mechanism. |
Crushing Action: Inside the crusher, a rotating rotor equipped with blades or hammers spins at high speed. The blades or hammers impact the incoming material, breaking it into smaller pieces. |
Granulation: As the material is further processed, it is reduced to the desired size, typically in the form of flakes or granules. |
Discharge: The crushed and granulated material is discharged from the bottom of the crusher, often onto a conveyor belt or into a container for further processing or packaging. |
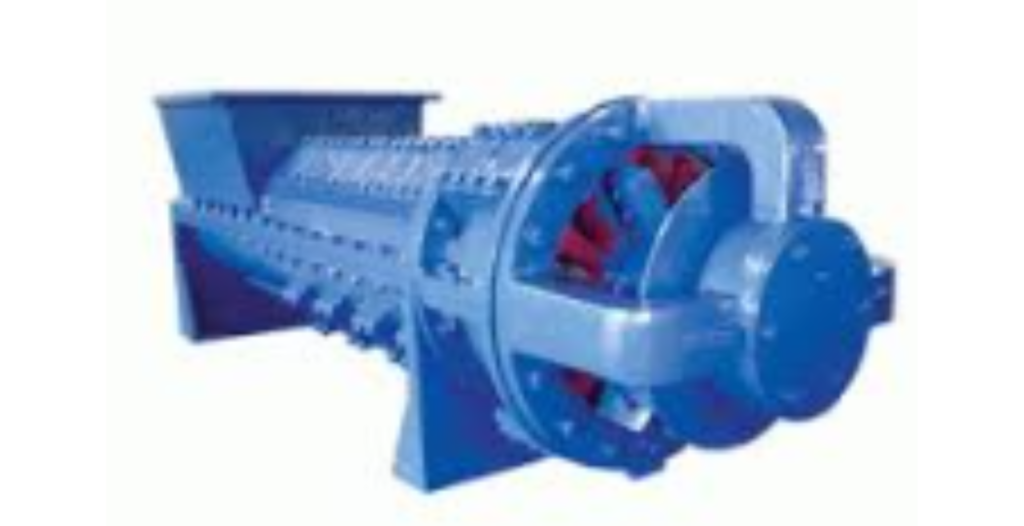
Advantages: |
Size Reduction: Flake Crusher Mills effectively reduce the size of materials, making them suitable for downstream processes or easier to handle. |
Uniform Granulation: These machines produce uniform and consistent particle sizes, ensuring product quality and process reliability. |
Customizable Output: The fineness of the output can often be controlled by adjusting the rotor speed or the size of the blades or hammers. |
High Capacity: Flake Crusher Mills are designed for high throughput and are suitable for processing large volumes of material. |
Versatility: They can process a wide range of materials, including dry powders, agglomerates, and even heat-sensitive or abrasive substances. |
Disadvantages: |
Initial Investment: Flake Crusher Mills can be expensive to purchase and install, particularly for heavy-duty or specialized models. |
Maintenance: The heavy-duty nature of these machines can result in high maintenance requirements, including blade or hammer replacement. |
Energy Consumption: Flake Crusher Mills can consume a significant amount of energy, especially when processing tough or hard materials. |
Noise and Vibration: The operation of Flake Crusher Mills can generate noise and vibration, which may require noise control measures. |
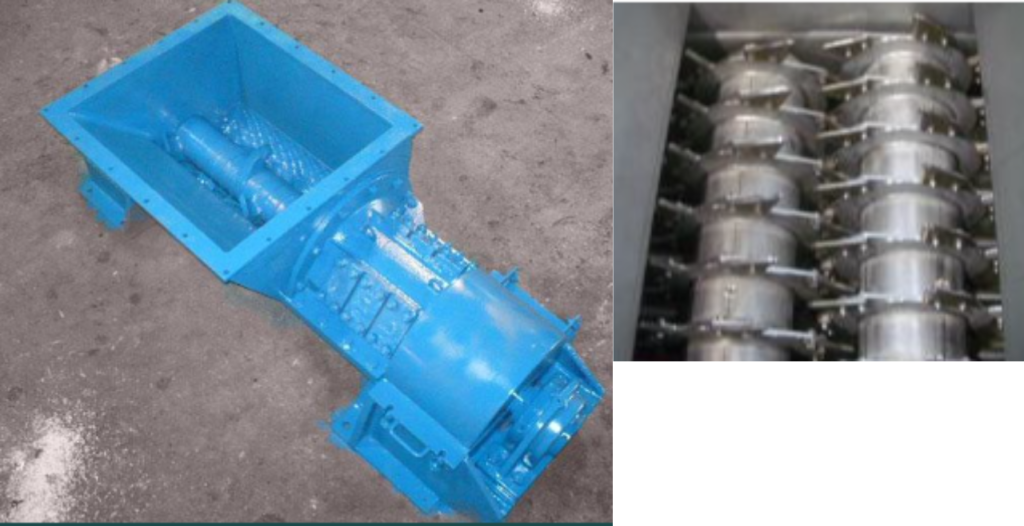
Applications: |
Flake Crusher Mills find applications in various industries, including: |
Food Industry: For size reduction and granulation of food ingredients like spices, grains, and sugar. |
Pharmaceutical Industry: For reducing the size of pharmaceutical powders and granulating solid dosage forms. |
Chemical Industry: In the production of chemicals and agrochemicals, as well as for breaking down agglomerates. |
Bulk Material Handling: For reducing the size of bulk materials such as plastic pellets, resins, or minerals. |
Recycling: In the recycling industry for size reduction of materials like plastics, rubber, and electronic waste. |
Materials of Construction (MOC): |
The choice of materials for Flake Crusher Mills depends on the specific application and the materials being processed. Common materials of construction include: |
Stainless Steel: Often used for the main structure and crushing components due to its corrosion resistance and suitability for food and pharmaceutical applications. |
Hardened Alloys: Used for blades or hammers that come into direct contact with the material to handle wear and abrasion. |
Summary: |
A Flake Crusher Mill is a size reduction machine that crushes and granulates materials into smaller flakes or granules. It operates by using a high-speed rotor with blades or hammers to impact and break down incoming material. Flake Crusher Mills offer advantages such as size reduction, uniform granulation, and high capacity, but they also come with considerations like initial investment, maintenance, energy consumption, and noise generation. Materials of construction are selected based on the specific application’s requirements. |