GRINDING/MILLING/PARTICLE SIZE REDUCTION TECHNOLOGY & PRODUCTS
Fine Impact Type Pin Mill
Fine Impact Type Pin Mill is a specialized type of grinding mill used for reducing the size of fine and brittle materials into very fine powders. These machines are often used in applications where precise control over particle size and shape is essential. Below is a detailed overview of Fine Impact Type Pin Mills, including their working principles, advantages, disadvantages, applications, materials of construction (MOC), and a summary: |
Working Principles: |
The working principle of a Fine Impact Type Pin Mill involves the following steps: |
Feeding: The material is introduced into the mill through a feeding mechanism, such as a hopper or screw conveyor. |
Impact and Attrition: Inside the mill, a high-speed rotor equipped with closely spaced pins or studs rotates. The material is subjected to intense impact and attrition forces as it passes through the narrow gap between the rotor and the stationary pins or studs. |
Size Reduction: The repeated impacts and collisions between the particles and pins reduce the material to a fine powder. The centrifugal force generated by the rotor helps to push the ground material through the screen or classifier to control the final particle size. |
Classification: Some Fine Impact Type Pin Mills have integrated classifiers or screens to separate the fine particles from coarser ones, ensuring that the desired particle size distribution is achieved. |
Discharge: The finely ground material is discharged from the mill, typically via a conveyor or directly into a collection vessel. |
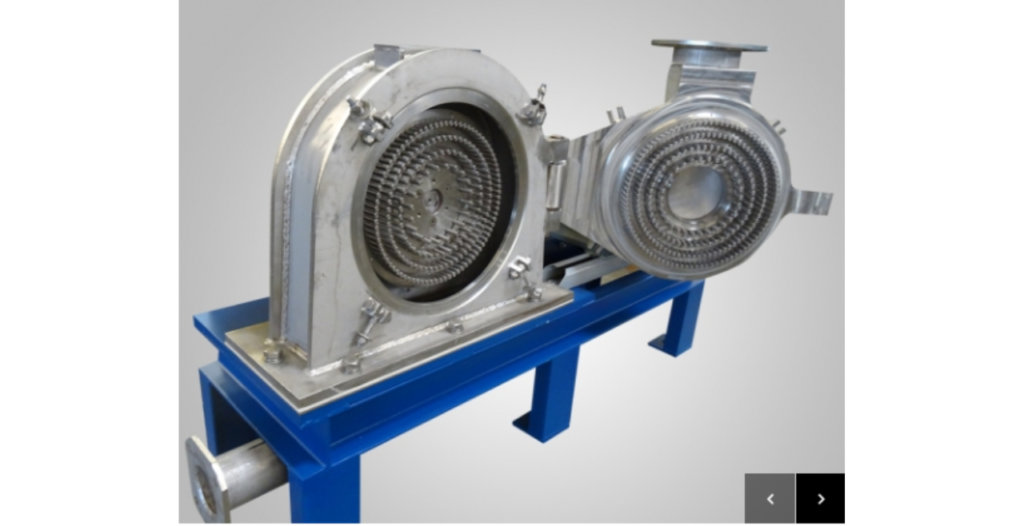
Advantages: |
Precise Particle Size Control: Fine Impact Type Pin Mills offer excellent control over particle size and distribution, making them suitable for applications requiring fine powders. |
Uniform Particle Shape: These mills produce particles with a uniform and well-defined shape, which can be crucial in some industries like pharmaceuticals and cosmetics. |
High Efficiency: Fine Impact Type Pin Mills are highly efficient at reducing the size of brittle materials with minimal heat generation. |
Low Heat Generation: Compared to some other grinding methods, they generate relatively low heat during operation, which is important for preserving heat-sensitive materials. |
Versatility: They can process a wide range of materials, including crystalline, brittle, and heat-sensitive substances. |
Disadvantages: |
Initial Investment: Fine Impact Type Pin Mills can be expensive to purchase and install, especially for specialized or high-capacity models. |
Maintenance: These machines can experience wear and tear on pins or studs, necessitating maintenance and replacement. |
Limited for Tough Materials: They may not be suitable for processing tough or elastic materials effectively. |
Dust Generation: High-speed impact can generate dust, which may require a dust collection system for hygiene and safety. |
Applications: |
Fine Impact Type Pin Mills find applications in various industries, including: |
Pharmaceuticals: For milling active pharmaceutical ingredients (APIs) and excipients to fine powders. |
Cosmetics: In the production of cosmetic powders with precise particle size and shape requirements. |
Chemicals: For reducing the size of chemicals, pigments, and dyes. |
Food Industry: For grinding spices, herbs, and food additives to fine powders. |
Minerals and Ceramics: In the processing of minerals, pigments, and ceramics for a controlled particle size distribution. |
Materials of Construction (MOC): |
The choice of materials for Fine Impact Type Pin Mills depends on the specific application and the materials being processed. Common materials of construction include: |
Stainless Steel: Often used for the main structure and grinding components due to its corrosion resistance and suitability for food and pharmaceutical applications. |
Hardened Alloys: Used for pins, studs, or other components that come into direct contact with the material to handle wear and abrasion. |
Summary: |
A Fine Impact Type Pin Mill is a specialized grinding mill used for reducing fine and brittle materials into very fine powders. It operates by using a high-speed rotor with closely spaced pins or studs to impact and break down the material. These mills offer precise particle size control, uniform particle shape, high efficiency, and low heat generation. However, they come with considerations like initial investment, maintenance, limited suitability for tough materials, and dust generation. Materials of construction are selected based on the specific application’s requirements. |