Pharmaceutical Technology/Products
Stirrer Type Vessels
Stirrer type vessels, also known as stirred tanks or stirred reactors, are industrial vessels equipped with mechanical agitators or stirrers used for mixing, blending, and various chemical processes in industries such as chemical engineering, pharmaceuticals, food processing, and biotechnology.
The working principles of stirrer type vessels involve the following key aspects:
Design: Stirrer type vessels typically have a cylindrical or conical shape with a flat or dished bottom. They are equipped with one or more agitators or stirrers, which are mounted on a shaft that extends into the vessel.
Agitation: An electric motor or another power source drives the agitator, causing it to rotate within the vessel. The agitator’s blades or impellers create turbulence and movement in the liquid or slurry, ensuring thorough mixing or blending.
Heat Transfer: Many stirrer type vessels are designed with jacketed walls or coils, allowing for precise temperature control through heating or cooling during chemical reactions or processes.
Batch or Continuous Operation: Stirrer type vessels can operate in batch mode, where materials are loaded, processed, and then unloaded, or in continuous mode, where materials are continuously fed in and products are continuously discharged.
Control and Monitoring: Process parameters such as agitation speed, temperature, pressure, and flow rates are monitored and controlled to achieve the desired process outcomes.
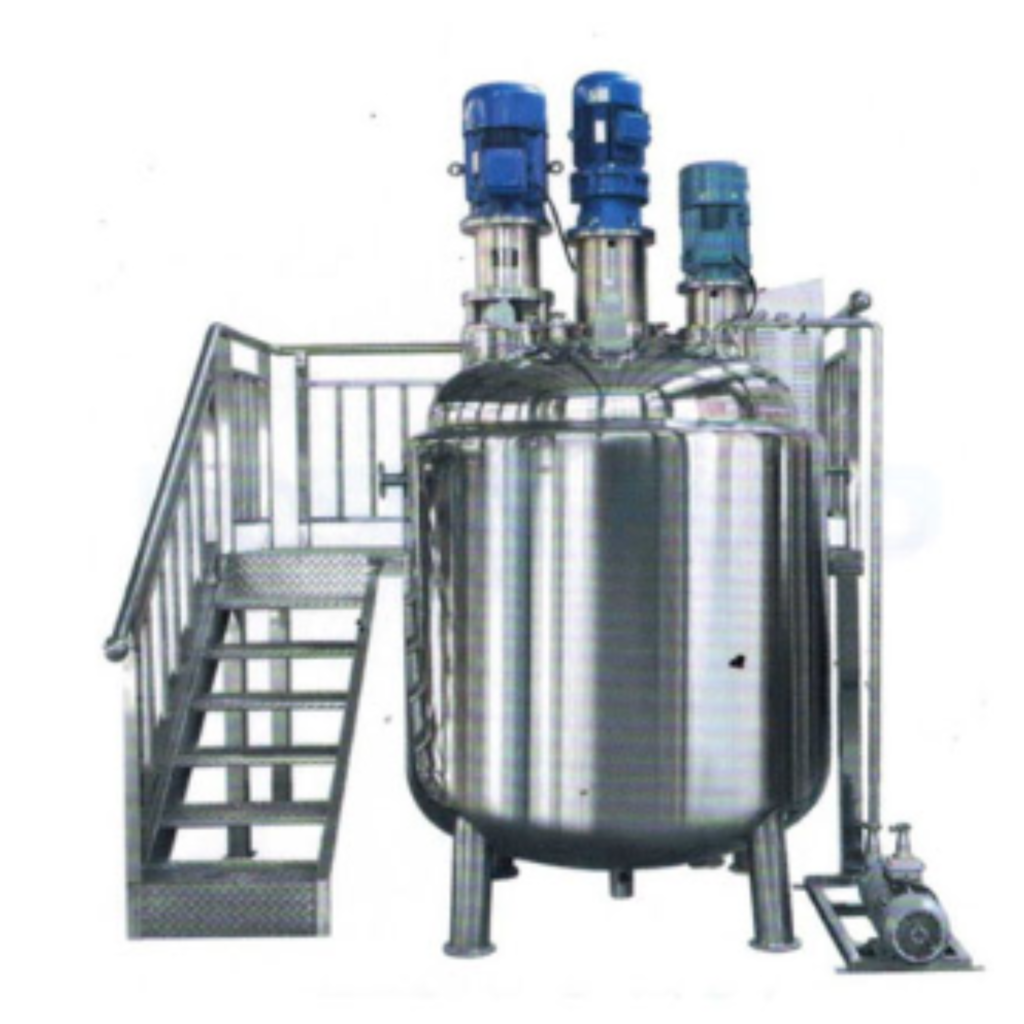
Advantages:
Efficient Mixing: Stirrer type vessels provide efficient and uniform mixing, ensuring homogeneity of the contents.
Temperature Control: Precise temperature control is possible, making them suitable for exothermic or endothermic reactions.
Versatility: These vessels can handle a wide range of viscosities, from liquids to highly viscous slurries, and are used for various processes, including mixing, dissolution, crystallization, and chemical reactions.
Scalability: Processes developed in laboratory-scale stirrer type vessels can often be scaled up for larger production using similar equipment.
Automation: Stirrer type vessels can be fully automated, reducing the need for manual labor and ensuring consistent process conditions.


Disadvantages:
Complexity: Stirrer type vessels can be complex to design, install, and operate, especially in large-scale industrial settings.
Maintenance: Regular maintenance of agitator systems and seals is required to ensure smooth operation.
Capital Cost: The initial cost of purchasing and installing stirrer type vessels can be significant, particularly for larger systems.

Applications: Stirrer type vessels find applications in a wide range of industries, including:
Chemical Processing: For chemical reactions, mixing of raw materials, and crystallization processes.
Pharmaceuticals: In drug manufacturing for mixing, blending, and reactions.
Food and Beverage: For mixing ingredients in food and beverage production.
Biotechnology: In bioreactors for fermentation processes in the production of bio-based products.
Water and Wastewater Treatment: In processes like flocculation, coagulation, and pH adjustment.

Summary: Stirrer type vessels are versatile industrial equipment used for mixing, blending, and chemical processes in various industries. They work by using mechanical agitators or stirrers to create turbulence and movement within the vessel, facilitating efficient mixing and temperature control. While they offer advantages such as efficient mixing and precise temperature control, they can be complex to design and maintain, and they often require a significant initial capital investment. Stirrer type vessels play a crucial role in processes ranging from chemical reactions to pharmaceutical manufacturing and food production.